Choosing The Best Vibration Sensor or Accelerometer
There are many benefits to using vibration sensors, or accelerometers in condition monitoring applications.
Implementing a predictive maintenance program that is based on information taken from vibration monitoring and analysis can greatly increase the reliability and improve the cost effectiveness of your plant. We take a look at how to go about selecting the best vibration sensor or accelerometer for your particular application.
Measuring the vibration of machinery is an excellent way of monitoring the health of your critical plant and equipment.
Historically, routine maintenance runs would have been scheduled, even when they weren't really required. There are two problems associated with this method of breakdown prevention. Firstly the cost associated with taking a critical piece of machinery off line unnecessarily. Secondly it introduces the risk of failure if an error is made during the maintenance job.
Nowadays automatic condition monitoring is used to monitor the health of machinery, so that maintenance tasks are scheduled according to need and not according to an arbitrary date in the calendar.
At the heart of condition monitoring is the measurement of the vibration of the machinery, or its critical parts.
How is this done?
Every rotating machine has its own unique vibration characteristics. Problems such as unbalance, or rolling element bearing damage cause the vibration characteristics to change. In most cases the manufactures of such machinery will be able to tell you what the normal vibration characteristics are.
As with most all other industrial sensors and transducers, it is critical that the vibration sensor, or accelerometer selected is well suited to condition monitoring applications. This is necessary to ensure that the acquired data is accurate and fit for purpose. Using an inappropriate device could result in unexpected plant failure or a reduction in the working life of a piece of machinery.
The first thing to ascertain is what do you want the sensing device to do and what environment or location will it be used in?
Choosing a vibration sensor or Accelerometer
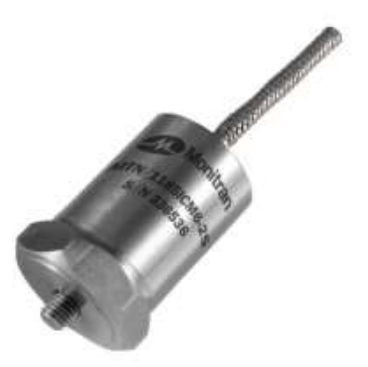
First of all do you want to continuously monitor the vibration levels of a machine? Or will you be carrying out vibration analysis and monitoring at regular intervals?
When it comes to protecting machinery and plant, the most effective system is a fully integrated condition monitoring system. For this type of installation, accelerometers with a DC output are more suitable.
This type of accelerometer produces an output proportional to velocity or acceleration in the range of 4-20ma. This means they can be used with most PLCs to continuously monitor plant equipment and machinery. Of course this can also extend to triggering an automatic shutdown of any machinery if necessary.
The next thing to consider is the frequency response of the accelerometer. Most general purpose vibration sensors (both AC and DC) frequency responses start at a little under 1Hz. This will be fine for the majority of industrial applications.
However, should your application be measuring the movement in a large structure, such as a bridge, then a dedicated low-frequency sensor that can measures down to DC (0Hz) is required. The upper limit of a general purpose accelerometer is typically about 12 kHz. If you need to go higher than this special purpose devices are available for frequencies up to 40 kHz.
After that you need to decide how small a change in output you wish to detect.
For example, one particular model of accelerometer may have an operating range of ±80g, but be available with different sensitivities. Let's presume that you are using a device, which has an operating range of ±80g and 100m/vg sensitivity. At full operating range this sensor will output -8v~+8V, with a 1g change of acceleration corresponding to a 100mv change.
If this sensor was only going to be used to monitor vibrations of around ±8g, then you may find that this is not enough of a change in the output. In which vase it would be much better to opt for an accelerometer with a sensitivity of 1V. This is because the change of 1g would correspond to a change of 1V instead, making it easier to monitor.
The 4-20mA output from the accelerometer can be connected to either a PLC, or simple display/controller unit so that when a change from the normal vibration characteristic is detected an alarm is given.
In some applications you may need to do more in depth machine analysis. If this is the case, then we would recommend using a vibration sensor, such as the MTN/1186. This has two outputs, a standard 4-20mA gross vibration signal, plus an AC vibration waveform. The 4-20mA signal can be used for gross monitoring by a PLC and can be used, for example to shut down a fan motor if anything goes wrong and will prevent gross damage.
The AC vibration wave form can be used with an FFT (Fast Fourier Transform) analyser to see the various frequency components. Some things like bearing failure for example, will generate frequencies much higher than the usual rotation rate. If a ball bearing has 36 balls in it, the frequency component of a failing ball will be an output vibration signature with a harmonic component 36 times the base rotation frequency. While it may not add a lot to the final amplitude, which means the 4-20mA signal won't see much difference, the AC vibration waveform will allow you to see it with an FFT analyser.
Hand Held Vibration Meters
One problem we often run into is how to know how many mm/s vibration to use as a full scale, if the machine manufacturer can't give you this information then using a small scale plant a hand held vibration meter like the Lutron VB-8206SD may be the answer. This can give you on the spot measurements, so you know which accelerometer you need. It is also ideal for the field monitoring of a single piece of machinery, when you cannot justify the expense of installing a fixed condition monitoring system. The data can be recorded onto an SD card and analysed in a spreadsheet.
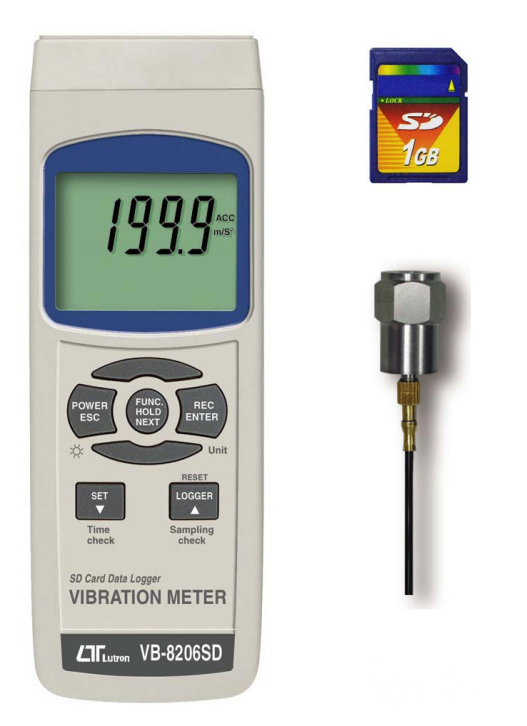
Vibration sensors or accelerometers with AC outputs, such as the Monitran MTN/2200 are ideal for analysis tasks. This is because the output can easily be fed into a spectrum analyser or oscilloscope, allowing you to gather data on the amplitude and structure of the vibration.
So far, we have presumed that the accelerometer is going to be used in a general purpose industrial application.
Environmental Considerations
However, this will not always be the case. Some applications may dictate that the accelerometer has to be able to withstand factors such as high temperature, water, humidity and hazardous atmospheres. Monitran manufacturer accelerometers with certain characteristics, such as devices that are sealed to IP67 or 68, or have high or low operating temperatures.
For hazardous areas intrinsically safe devices with IECEx certification, or devices that have been approved by Simtars to ANZex standards need to be used.
Last but not least there is the physical space available and ease of access.
Where you are going to mount the accelerometer will generally dictate if you need side entry cable, or top entry cable.
It is becoming more common to use a vibration sensor that has a connector. The reason being that there is a belief that saves time and costs, should it be necessary to remove the accelerometer for maintenance purposes. However, it costs significantly more for the initial connector installation, so direct cable will always give you a lower installed price as well as perfect reliability.
Using connectors on the accelerometer is not recommended for heavy vibration applications. This requires armoured cable directly connected to the accelerometer. With modern cable ties, removing a sensor isn't difficult, and it will reward you with lower cost and better reliability. This is because the connector will always be the weak point in the installation. The soldered joints inside the connector are prone to failure. Direct cable embedded in epoxy filling will ensure longer life.
It is vital that the accelerometers you end up using are fit-for-purpose, as they are often used to protect equipment that not only has a high capital cost, but are also used to prevent costly and disruptive shut downs.
A well-designed condition monitoring system, which includes the use of vibration monitoring and analysis reduces the need for costly, unscheduled plant shutdowns.
We have seen a case at a sewage treatment plant, where a series of large ventilation fans were not fitted with vibration monitoring. A blade on one fan developed a fault and the resulting vibration destroyed the fan cabinet, the fan motor, and severely damaged the two adjacent fan cabinets. The total repair bill exceeded $250,000!
A few accelerometers and a small PLC would have been far cheaper.
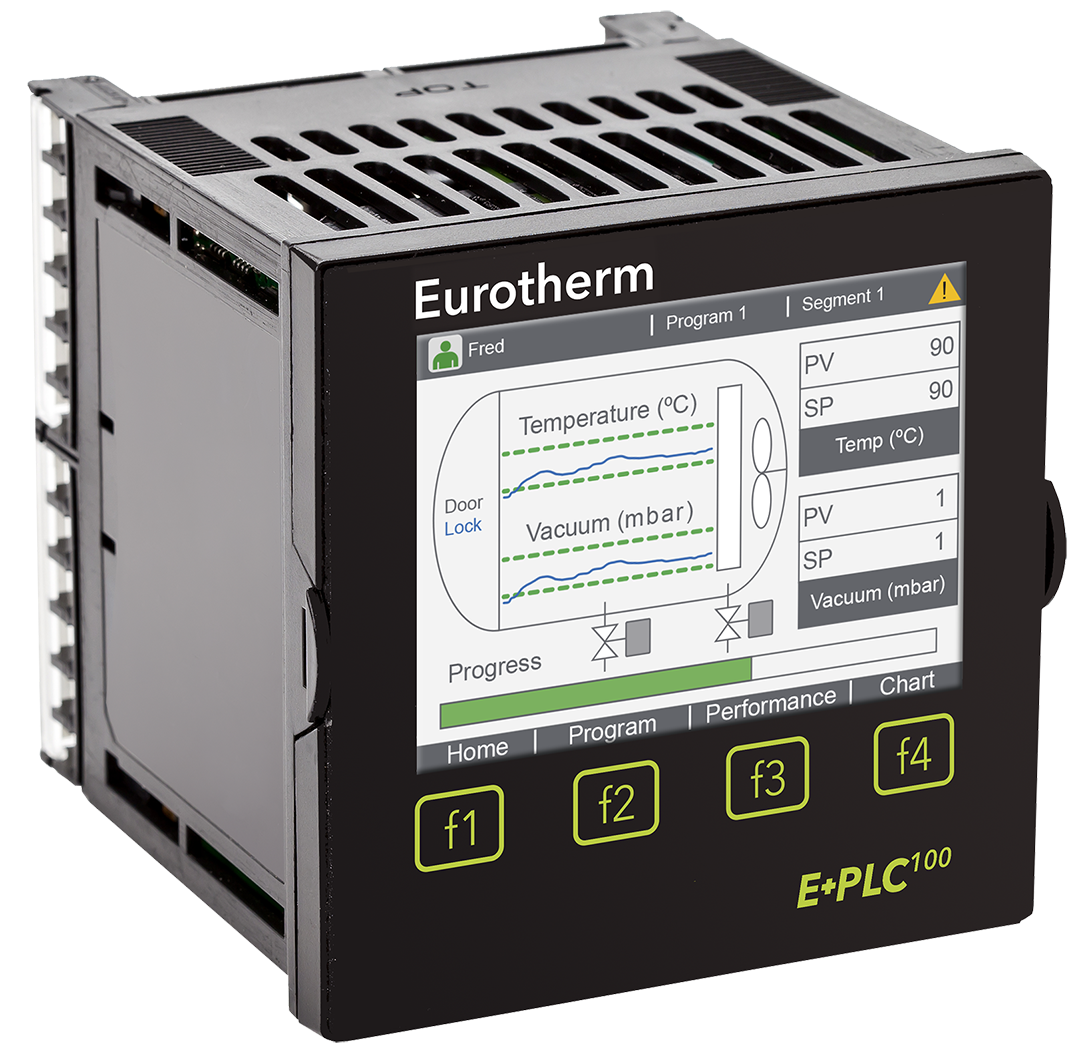
If you would like assictance in selecting a suitable acceleorometer for your application, or a small PLC then contact ADM Instrument Engineering.
A member of our expert team will gladly answer any questions that you may have.
WAS THIS INFORMATION USEFUL?
Why not share it with you industry peers on LinkedIn? Simply click on the blue LinkedIn share icon below.