Harting Contacts and Termination Techniques
Harting manufactures diverse types of contacts – screw, crimp, cage-clamp, solder (circular), axial and IDC.
The most common termination techniques apply to Harting Han connectors and can be used in various industrial applications. Choosing the right technique depends on the type of cable, cable cross-section, as well as the number and type of contacts, as they offer different advantages for varying production conditions.
The main difference between contact and termination is that contact is the product, whereas termination is the method of using the contacts.
Common Types of Harting Terminations
Screw – This termination is a type of electrical connection where a wire is secured by tightening a screw. With screw terminations, the wire is crimped onto the male contact/contact sleeve of the circular connector using a screw. The technique is simple and effective and does not require any special tools. Screw termination can also be used for stranded wires.
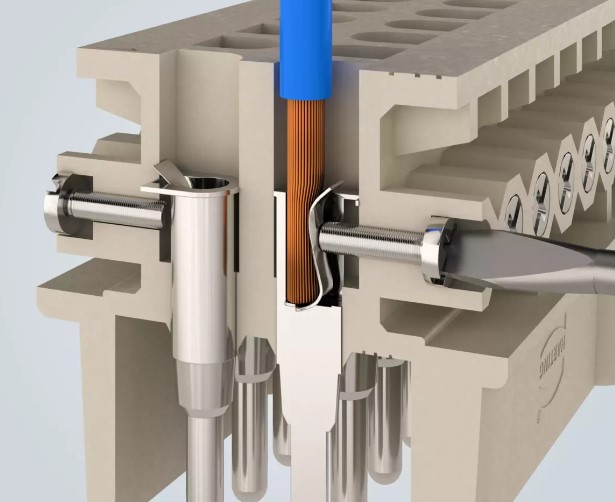
Crimp - In crimping terminations, a wire is enclosed in a gas-tight manner within the crimp contact by controlled deformation with crimping pliers or hydraulic/pneumatic crimping tools. This technique essentially produces a cold weld, which ensures optimum resistance to deterioration and mechanical stress from shock and vibration.
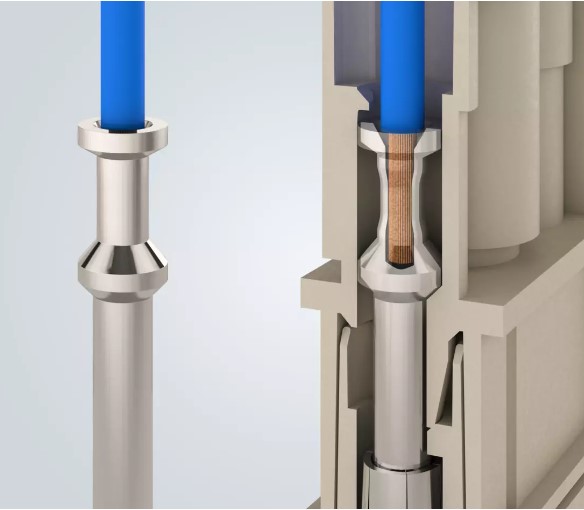
Cage-clamp – This type of termination requires very little wire preparation, and without the need for special tools. It is a low-cost installation method with a high degree of mechanical security. Cage-clamp is also vibration proof because the wire/conductor and the screw are in the same location.
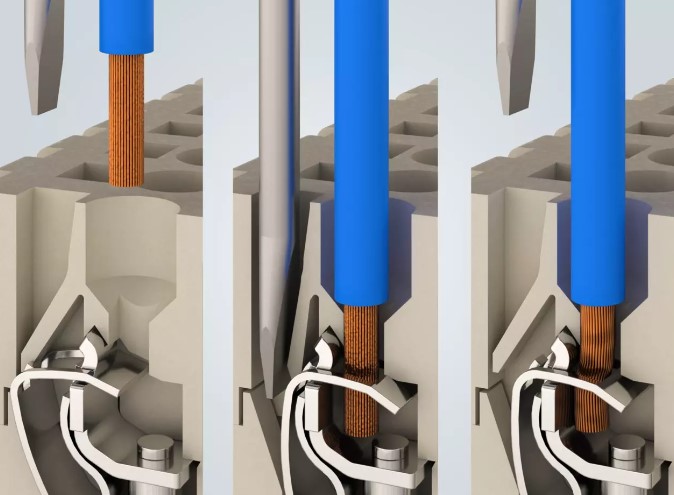
Solder - There are two kinds of solder termination technologies – Through Hole Reflow (THR) and Through Hole Technology (THT).
Reflow is a process that involves heating solder to bond components to a printed circuit board (PCB).
THR Soldering
With THR soldering technology, the connector is inserted – similar to conventional assembly method – into through-plated PCB holes, which can be done by pick-and-place machines. The THR components are then soldered together with the pieces placed on the surface as part of a common reflow procedure.
This technique features outstanding mechanical strength, made possible by a design adapted to the reflow soldering process (e.g., the use of high-temperature plastic).
THT Soldering
This is a conventional soldering technology, which has been used and proven for decades. In this method, the soldering pins of the connectors are inserted into through-plated PCB holes and then automatically and simultaneously wave soldered (bulk soldered) to other components.
Reflow
Surface Mounted Technology (SMT) connectors, in contrast to THT technology, do not have wire terminals, but are soldered directly to the solder pads on the PCB surface. This procedure is used for circuit board placement based on a uniform termination technique. It offers advantages as the use of SMT connectors eliminates the need for separate wave soldering.
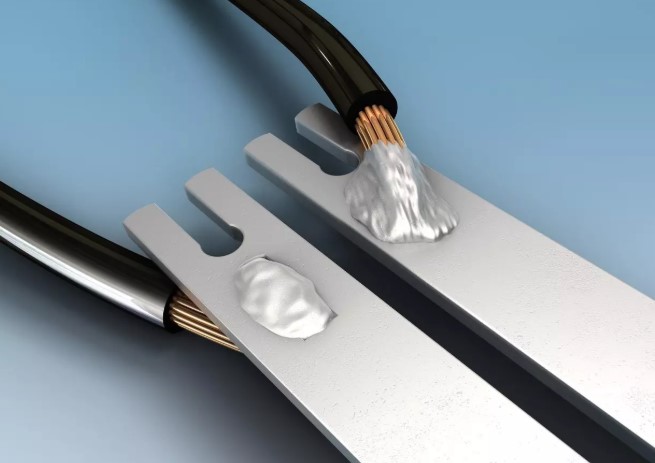
Axial – This termination combines the simple handling of the screw termination technique with the minimal space requirements of crimp contacts. This can be installed without any special tools, and is suitable for finely stranded wires with large cross-sections.
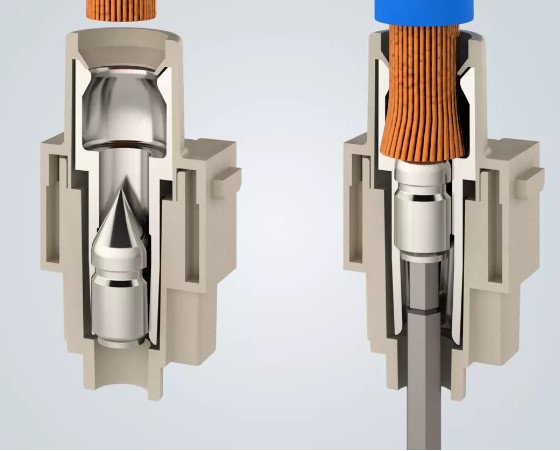
IDC – Insulation Displacement Connector (IDC) is quick and easy to connect, without soldering, screwing, or stripping. This is applicable for solid wires, especially those with small cross-sections.
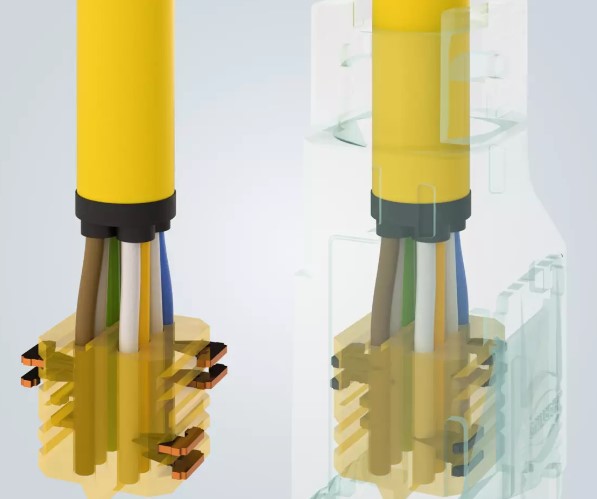
To view our Harting Han contacts and terminations, please check our webstore. If you cannot find what you are looking for, or are unsure of your application requirements, you can contact our team here for technical advice.