Master-Slave Network Operation of the Invertek Optidrive P2 VFD
The Invertek Optidrive P2 Variable Frequency Drive (VFD) features a master-slave network function, allowing up to 63 drives to operate in synchronisation on a single communications network. This function enables precise control across multiple drives by transmitting operating states and speed setpoints from one master drive to connected slave drives.
Here’s a detailed look at the master-slave operation, setup steps, key benefits and applications of using this functionality with the Optidrive P2.
Understanding the Master-Slave Function
In a master-slave configuration, a single "Master" drive (addressed as Drive 1) controls multiple "Slave" drives, which follow its operational state and speed frequency. The master drive sends its status (e.g., start/stop) and output frequency every 30 milliseconds, ensuring that all connected slave drives respond in unison. This setup creates a synchronised "digital gearbox," beneficial in applications that require coordinated motion among multiple drives.
Steps to Set Up the Master-Slave Network
Setting up a master-slave network with Optidrive P2 involves the following key steps:
-
Physical Network Connection: Connect all drives using the RJ45 connectors provided on each Optidrive P2. Invertek provides various lengths of connection cables and splitters for this purpose. For networks with longer cable runs or a high number of slaves, install RS485 repeaters to maintain signal integrity.
-
Address Configuration: Assign a unique address to each drive using Parameter P5-01. The master drive must always be assigned address 1. Slave drives should have addresses greater than 1, but these do not need to be consecutive.
-
Master Drive Setup: The master drive should be configured according to the application requirements. It can operate in any mode except slave mode, so set P1-12 to any value other than 5.
-
Slave Drive Configuration:
-
Address Assignment: Set each slave drive's unique address in P5-01.
-
Operating Mode: Configure each slave to operate in slave mode by setting P1-12 = 5.
-
Minimum and Maximum Speeds: The speed of each slave will be limited by its programmed minimum and maximum speed parameters.
-
Ramp Times: Ensure the slave’s acceleration and deceleration ramp times are set to match or exceed those of the master drive.
-
-
Speed Scaling and Offset Configuration: The slave drives can apply scaling and offsets to the master’s frequency output, using parameters P2-28 and P2-29. These settings allow flexible adjustments to the slave speeds relative to the master, with options for fixed scaling or analog input adjustments.
Key Parameters for Master-Slave Configuration
-
P5-01: Drive Address (set to 1 for the master, unique values >1 for each slave).
-
P1-12: Operating Mode (set to 5 for slaves).
-
P2-28 and P2-29: Digital Speed Scaling Source and Scaling Factor, respectively, allowing for scaling adjustments based on the master’s frequency output.
-
P1-03 and P1-04: Acceleration and Deceleration Ramp Times, ensuring coordinated ramping between the master and slaves.
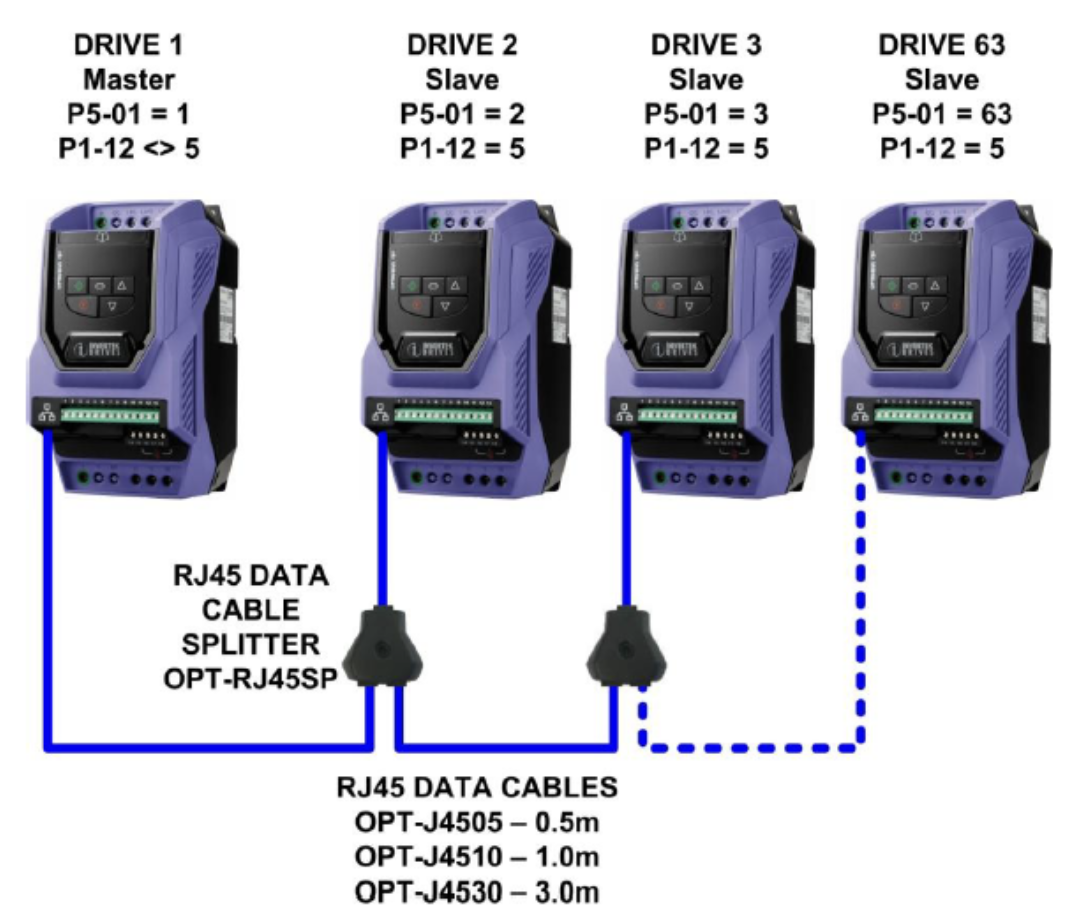
Benefits of Using the Master-Slave Function
Using a master-slave setup offers several advantages, particularly for systems with multiple synchronized motors, such as conveyor belts, air handling systems, or machine tools that require unified control. Benefits include:
-
Synchronised Operation: Slave drives seamlessly match the operational state and frequency of the master drive, ensuring consistent performance across multiple drives.
-
Flexible Scaling: Slave speeds can be scaled to match specific needs, allowing precise control in applications that require variable speed ratios between drives.
-
Streamlined Control: A single command sent to the master drive initiates the start or stop function for all slaves, simplifying operational control in complex systems.
Applications of the Master-Slave Function
This setup is especially useful in applications such as:
-
Conveyor Systems: Ensuring multiple conveyors operate at the same speed for smooth material flow.
-
Air Handling Units: Where multiple fans are needed, with one potentially operating at a slightly reduced speed to control airflow dynamics.
-
Machinery with Speed Adjustment Requirements: Where the operator needs to adjust speed offset, such as in systems requiring fine-tuned speed control.
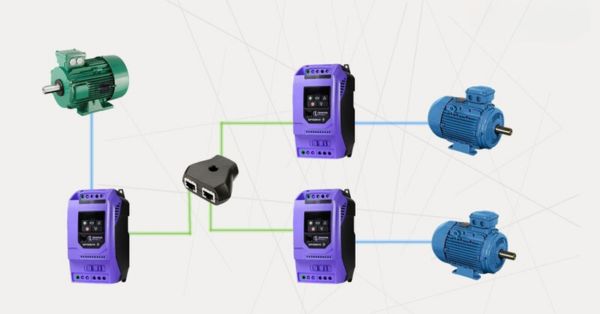
Additional Features of the Master-Slave Operation
1. Enable/Disable Control of Individual Slave Drives
Each slave drive in the network requires an enable signal, typically set up on Digital Input 1 (terminal 2). This means that each slave can be independently enabled or disabled by controlling this input. During operation, if Digital Input 1 on a slave drive is opened, the drive will decelerate to a standstill based on the deceleration rate set in Parameter P1-04.
2. Acceleration and Deceleration Ramp Synchronisation
Each slave drive in the master-slave network is governed by its internal acceleration and deceleration ramp times, configured in Parameters P1-03 and P1-04. By default, slave drives should ideally match the ramp rates of the master drive to maintain synchronization. However, in cases where different ramp times are required, these ramp times can be set differently for each slave.
3. Dynamic Speed Scaling and Offset Adjustment
The Optidrive P2 enables advanced speed scaling and offset adjustments for each slave drive, allowing individual slave speeds to be set as proportional to the master drive’s speed. This adjustment is managed through Parameters P2-28 (Digital Speed Scaling Source) and P2-29 (Digital Scaling Factor), which allow for a variety of scaling configurations, such as
-
Mixed Digital Scaling
-
Analog Offset Scaling
-
Combined Digital and Analog Scaling
OptiTools PC Software
OptiTools Studio is Invertek’s PC software designed for the efficient setup, monitoring, and control of Optidrive P2 VFDs, including master-slave network configurations. With OptiTools, users can configure parameters for multiple drives simultaneously, manage drive settings, and monitor real-time performance, which streamlines setup and reduces configuration time.
Key advantages include the ability to centrally manage and troubleshoot the entire network, saving time and minimising errors. OptiTools' real-time diagnostics facilitate rapid adjustments, making it an essential tool for optimising master-slave networks in complex systems.
The master-slave function in the Invertek Optidrive P2 offers a robust solution for applications requiring synchronised drive control. By leveraging OptiTools Studio for setup and monitoring, users can efficiently configure, control, and optimize drive networks to meet the demands of complex applications.
Whether for conveyors, fans, or machinery requiring coordinated motor speeds, the Optidrive P2’s master-slave capabilities provide an efficient and flexible solution, simplifying control while enhancing performance.