Waterproof Variable Speed Drives for Washdown Areas
Understanding Washdown Applications
Industries and processes that require a high degree of cleanliness and sanitation needs to be cleaned on a regular basis. This usually involves the washdown procedure, which makes the process efficient and effective. Industries that require hygiene to be up most important are pharmaceuticals, and food and beverage processing plants. So that contamination, bacterial growth, and product spoilage is prevented, these industries and the corresponding applications require machinery and equipment that can withstand frequent and thorough washdown procedures.
The Washdown Procedure
The washdown procedure typically involves high pressure water jets, steam, and chemical cleaning agents, so that contaminants and residues are eliminated from all work surfaces. The following are the steps that are commonly followed:
- Pre-rinse: This is the first water spray used to remove residues and loose debris.
- Cleaning agents: These detergents and cleaning agents breaks down both organic and inorganic pollutants.
- Scrubbing: Surfaces with stubborn pollutants or debris require scrubbing by machine or by hand.
- Final Rinse: Any remaining cleaning agents and contaminants that have been dislodged and remaining on surfaces are cleaned out using water.
- Sanitisation: To guarantee microbial control, extra chemicals or heat treatment may be used.
- Sanitisation: To take a further step, extra chemicals or heat treatment may be used to promote or guarantee microbial control.
- Drying: Equipment that is dried using compressed air or air dried.
Requirements for Components in Washdown Applications
Washdown components must adhere to strict specifications because of the exposure to moisture, harsh chemicals, and high-pressure cleaning:
- Ingress Protection (IP) Rating: To guard against dust and water intrusion, equipment needs to have a high IP rating, such as IP65, IP66, or IP69K.
- Corrosion Resistance: To resist chemical exposure, materials such as stainless steel or speciality coatings must be utilised.
- Sealed Enclosures: To prolong the life of internal components, enclosures must be made to stop water intrusion.
- Hygiene Standard Compliance: Equipment needs to meet industry standards, like the FSANZ food safety regulations.
- Temperature Resistance: Because of refrigeration or steam cleaning, certain settings call for equipment that can withstand extremely high or low temperatures.
Role of Waterproof Variable Speed Drives (VSDs) in Washdown Applications
Water-resistant variable speed drives (VSDs), like those made by Invertek, are essential in washdown applications. This is because they maximise the performance and efficiency of motors used in a variety of processes. They contribute in the following ways:
- Efficiency in Energy Use
By modifying motor speeds in response to demand, VSDs lower energy usage. This is especially helpful in applications where full-speed operation isn't always required, like fans, pumps, and conveyor systems. - Accurate Management
Speed, torque, and acceleration can all be precisely adjusted with VSDs, guaranteeing the efficient running of operations like mixing, conveying, and packaging—all of which are essential in sanitary settings. - Less Damage and Wear
VSDs prolong the life of motors and other mechanical parts by preventing sudden starts and stops, which lowers maintenance expenses and downtime. - Designs That Are Sealed and Washdown-Ready
With their high IP ratings and sealed enclosures, modern VSDs made for washdown applications are guaranteed to survive exposure to harsh cleaning agents and direct water. - Improved Automation of Processes
By integrating VSDs into automation systems, production lines can be precisely controlled, and performance metrics can be tracked in real time.
There are other things to keep in mind as well. Such as an IP20 VSD can be mounted in a IP65 enclosure. As the long as the door is securely closed, the drive will remain functional. Failure to do so, like an electrician not closing the door properly after they have done the work, will have some consequences. If this happens, there will be water ingress on to the enclosure and afterwards on the drive as well, causing it to fail and likely cause a risk of electrical shock.
Although the drives themselves are waterproof, it doesn’t make the plastic of the drive’s enclosure resistant to caustic materials. The plastics cover of an Invertek IP66 VSD drive is a lot less susceptible to the corrosion that would be experienced by a standard steel cabinet.
Examples of VSD Use in Washdown Applications
- Processing of Food and Drink
- Conveyor Systems: VSDs control the speed of conveyor belts to minimise product waste and maximise food handling and packaging.
- Blenders and mixers: They ensure adequate ingredient mixing without overprocessing by offering controlled acceleration and deceleration.
- Processing Dairy Products
- Milk Pumps: To regulate flow rates and lessen mechanical stress and excessive foaming, VSDs modify pump speeds.
- Centrifugal separators are used to effectively separate cream from milk by maintaining precise speeds.
- Manufacturing of Pharmaceuticals
- Tablet Coating Machines: To guarantee consistent coating, VSDs provide exact control over drum rotation speeds.
- Liquid Filling Systems: They control pump function to ensure precise liquid dosage in bottles and vials.
- Processing of Poultry and Meat
- Equipment for deboning and cutting: VSDs modify motor speeds to achieve precise cutting, lowering waste and enhancing security.
- Refrigeration and cooling systems: These systems maximise compressor speeds to keep the right temperature.
For more information on Invertek drives and their weatherproof and IP rated drives, please read the below article:
Conclusion
Equipment used in washdown applications needs to be able to endure rigorous cleaning processes without losing functionality or dependability. In these applications, Invertek's Waterproof Variable Speed Drives are essential because they increase energy efficiency, improve process control, and guarantee hygienic standards are met. Waterproof VSD adoption will increase if industries prioritise automation and sustainability, propelling improvements in hygienic and productive production settings.
If you would like assistance in selecting a suitable variable speed drive for your application, please do not hesitate to contact ADM for friendly and helpful advice.
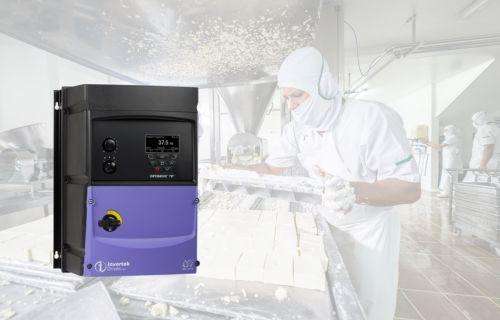