Process Controllers
In this blog post we give you an overview of ADM's wide range of process controllers. We carry stock of the most commonly used models.
Process Controller with Ethernet I/P and Modbus TCP/IP Master
The Eurotherm EPC2000, which is ideal for applications where you need a programmable single loop temperature, or process controller.
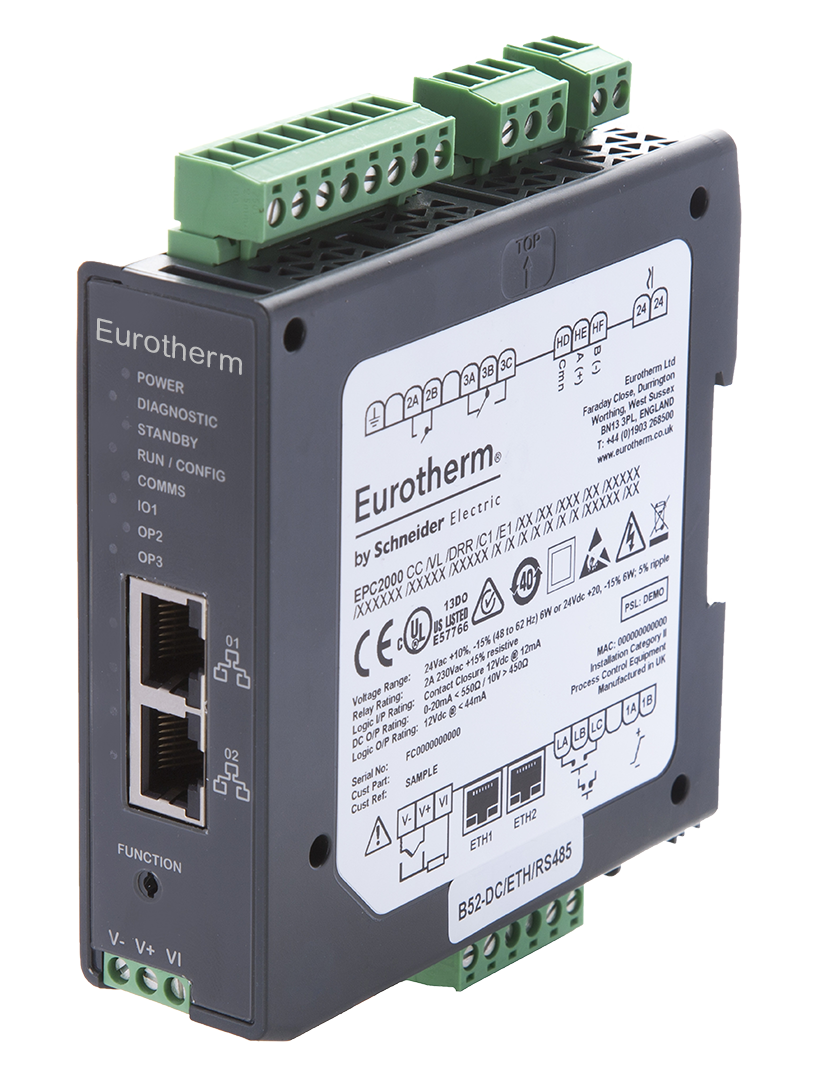
The EPC2000 is a highly cost-effective process controller as it does not sport any display panels, or HMI panels that you may not need. However, it is compatible with Eurotherm’s Proface HMI touch panels. So, it is a highly flexible solution that suits many different applications.
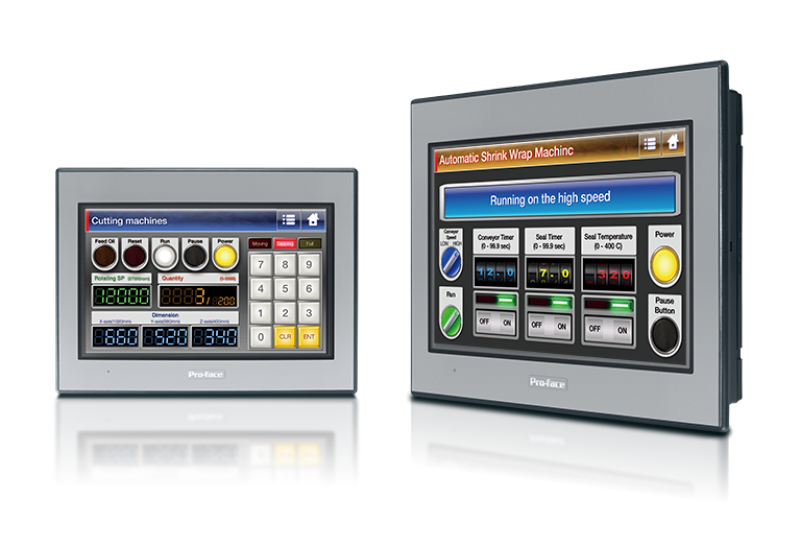
New Features
Eurotherm has updated the EPC2000 series process controllers, so that EtherNet/IP and Modbus TCP/IP Master are available.
Ethernet I/P
With the EtherNet/IP Server option, the EPC2000 Programmable Controller can be easily integrated with an existing instrument network to provide precision control to a PLC.
The EtherNet/IP is a 'producer-consumer’ communication system, which allows industrial devices to exchange time-critical data. This can be simple I/O devices such as sensors and transducers, or complex control devices such as robots and PLCs. The producer-consumer model allows the exchange of information between a single sending device (producer) and several receiving devices (consumers) without having to send data multiple times to multiple destinations.
Modbus TCP/IP
The Eurotherm EPC2000 can be configured to act as a master with up to three TCP and/or RTU slave devices.
A maximum of 32 data points is supported, which are shared amongst the configured slave devices.
These features make the EPC2000 a very attractive, and affordable option if you need to add additional I/O capability to your existing control system, or if you are building a ‘blind’ control system where no visual display is required.
Improved Quality, Reduced Scrap, Increased Profits
The Eurotherm EPC2000 gives you precise control and measurement performance.
You will enjoy a fast PID response, with minimal overshoot and oscillation, resulting in a high degree of control accuracy of the temperature, or process. Precise repeatable control improves the quality of the end product and reduces waste.
There is a convenient multi-programmer function, with up to 20 multi-step sequences. So the EPC2000 can be used to control relatively complex processes.
Eurotherm’s user function block wiring with optional maths, logic, totaliser and specialised functions enable you to use the EPC2000 to control additional system functions beyond PID control.
Lower Equipment and Maintenance Costs
The Eurotherm EPC2000 is DIN rail mountable and is simple to install, commission and replace.
There is no battery, so you don’t have to worry about monitoring battery levels. Yet the design is highly robust and offers excellent reliability in demanding environments and highly regulated industrial processes.
Eurotherm’s iTools software makes configuration and commissioning a relatively simple task. So is re-configuration, making the EPC2000 easy to adapt in line with your changing needs. Reduced installation, configuration and commissioning time vastly reduces installation and ongoing maintenance costs.
Try Before You Buy
Eurotherm’s iTools can be downloaded for free from the ADM Instrument Engineering website. It can be used as a simulator and training tool, giving you the opportunity to test if the EPC2000 is going to be the right solution for your application.
You can download iTools by following the below link:
Communications
The EPC2000 features a dual Ethernet switch, which gives you high-speed Ethernet connection, with an integral switch for daisy chain connection to supervisors, panels or PLCs.
There is also a serial port for added connectivity.
Inputs and Outputs
The available inputs and outputs are detailed in the below table.
The universal input is precise (0.1%) with a 50ms sample rate. This can be used for thermocouples, resistance thermometers, as well as mA, mV and V output devices.
Type | Description / Quantity |
---|---|
Analogue | 1 Universal Input |
Form A Relay Output | 1 |
Form B Relay Output | 1 |
Logic IO (SSR Drive) | 1 (mutually exclusive with DC Output) |
DC Output | 1 (mutually exclusive with Logic IO) |
Contact Closure Logic Input | 2 |
Process Controllers for Effective PID Loop Control
Trying to control a PID loop with a PLC is not always easy. Naturally, most plant operators and integrators like to stick to the PLC brand that they are familiar with.
However, occasionally an application will arise where the existing PLC is probably not the best control solution available for managing PID control loops. You could save time and money by looking at a different piece of hardware to manage this task. This also has the advantage of freeing up the PLC processor.
Eurotherm specialises in PID loop control and has a cost-effective solution for almost any PID loop control application. Whether it is control of a single loop, multiple loops, cascade loops and loops within a sequential control program.
Eurotherm’s PID control algorithm is argued to be one of the most accurate in the industry and has had over 50 years of refinement.
In this article we give you a brief overview of some of the PID control solutions available from Eurotherm. If after reading this overview you would like further information, please call us on 1300 236 467.
A member of our expert team will gladly answer any questions that you may have.
Low Cost Straight Forward PID Loop Control
The Eurotherm Nanodac process / controller is the ideal option for applications where you need to control no more than 2 PID loops.
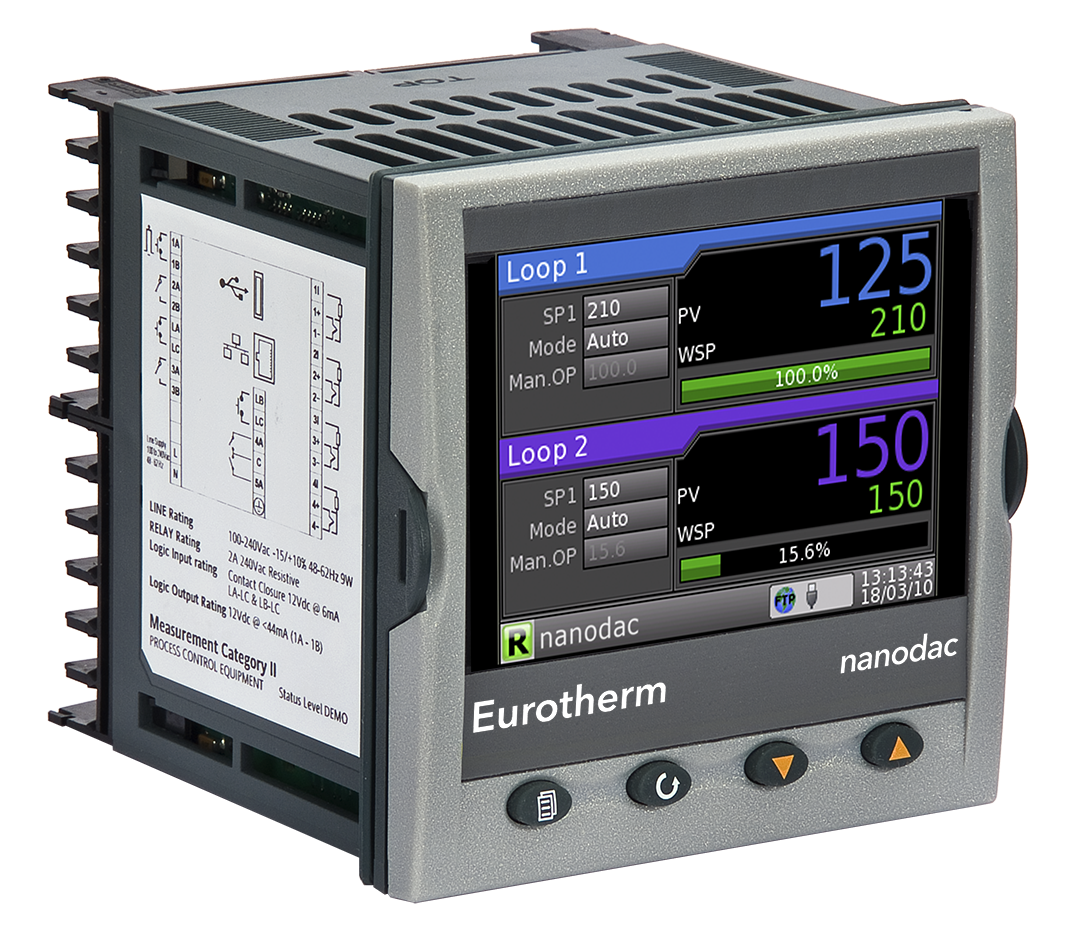
The Nanodac is a combined controller / graphic recorder, which features Eurotherm’s PID control algorithm.
The standard controls version of the Nanodac can control up to 2 PID loops and there is an advanced option, which allows you to control 2 PID loops and 1 cascade loop
Multiple Cascade Loops
The Eurotherm 2704 process controller is an advanced process controller that allows you to control up to 3 cascade PID loops.
The 2704 is a highly accurate and stable process controller available in a single, dual or triple loop format. It gives you some very useful features such as setpoint programming and a comprehensive selection of maths and logic functions.
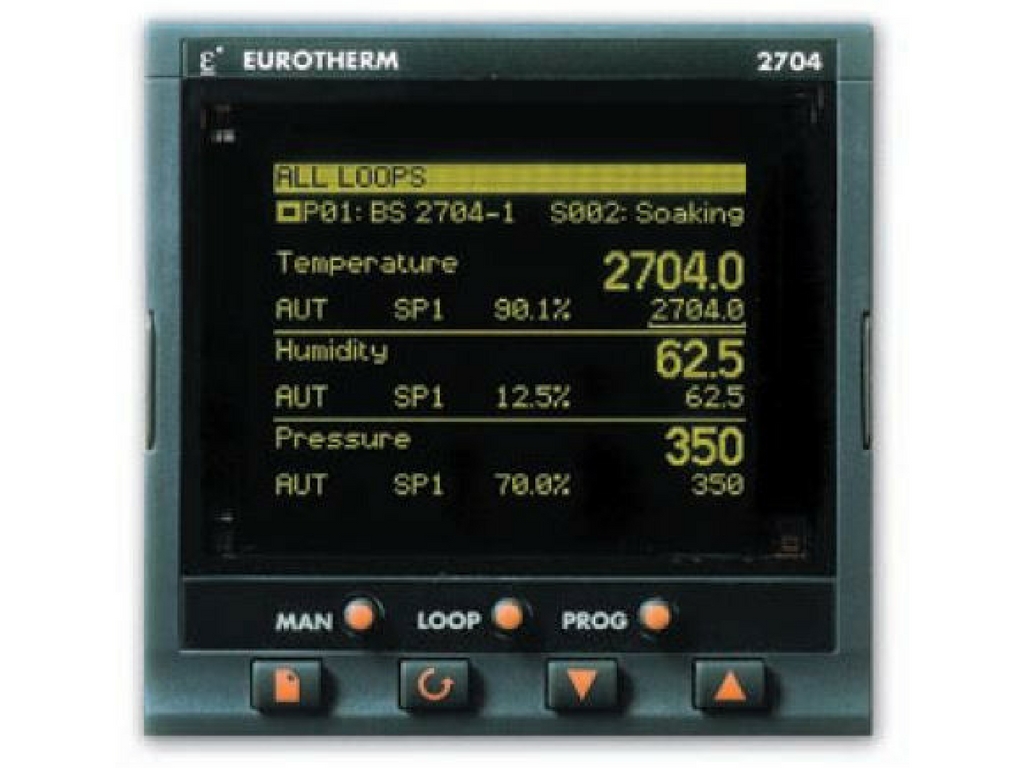
Controlling PID Loops & Sequential Control
The E+PLC 100 is a Eurotherm PID process controller with built-in PLC functionality.
This accurate PID controller allows for the process to reach a setpoint in the fastest possible time, with the least amount of overshoot. This translates into energy and operating cost savings.
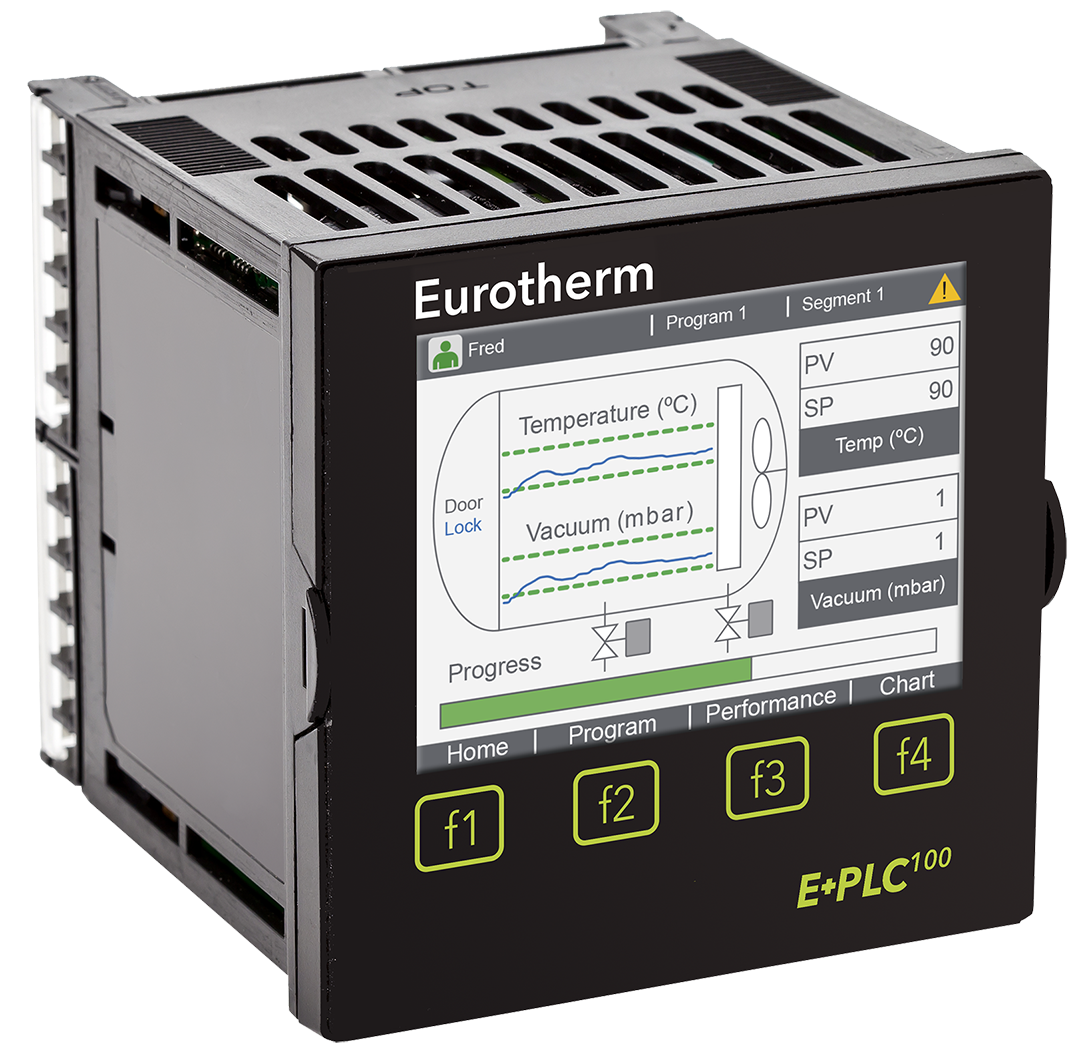
Implementing cascade control, where you have one control loop feeding into a second can be difficult to implement with most standard PLCs.
The Eurotherm PID control-based PLC allows this to be setup in a short space of time.
Programming
Of course, one thing that put many people off moving to a different brand of PLC is learning a whole new programming environment.
This may not be necessary with the Eurotherm E+PLC as it utilises the 3rd party programming environment CODESYS, which is provided free with the hardware.
More and more PLC manufacturers are boosting their development time, by putting this component of the PLC system in the hands the CODESYS specialist developers.
Therefore, more and more engineers are becoming familiar with it.
The fact that the Eurotherm E+PLC is IEC 61131 compliant makes it relatively easy to switch from other well-known brands.
Other manufacturers using CODESYS include: Eaton XC/XV, Wago, Beckhoff, ABB, Cutler Hammer, Weidmuller, to name a few.
Controlling 4 PID Loops or More
If you need to control 4 PID loops or more then the Eurotherm E-PLC 400 could be a more cost-effective solution. If required, this can be used in conjunction with Eurotherm’s E-HMI for applications where localised control and read-out is required.
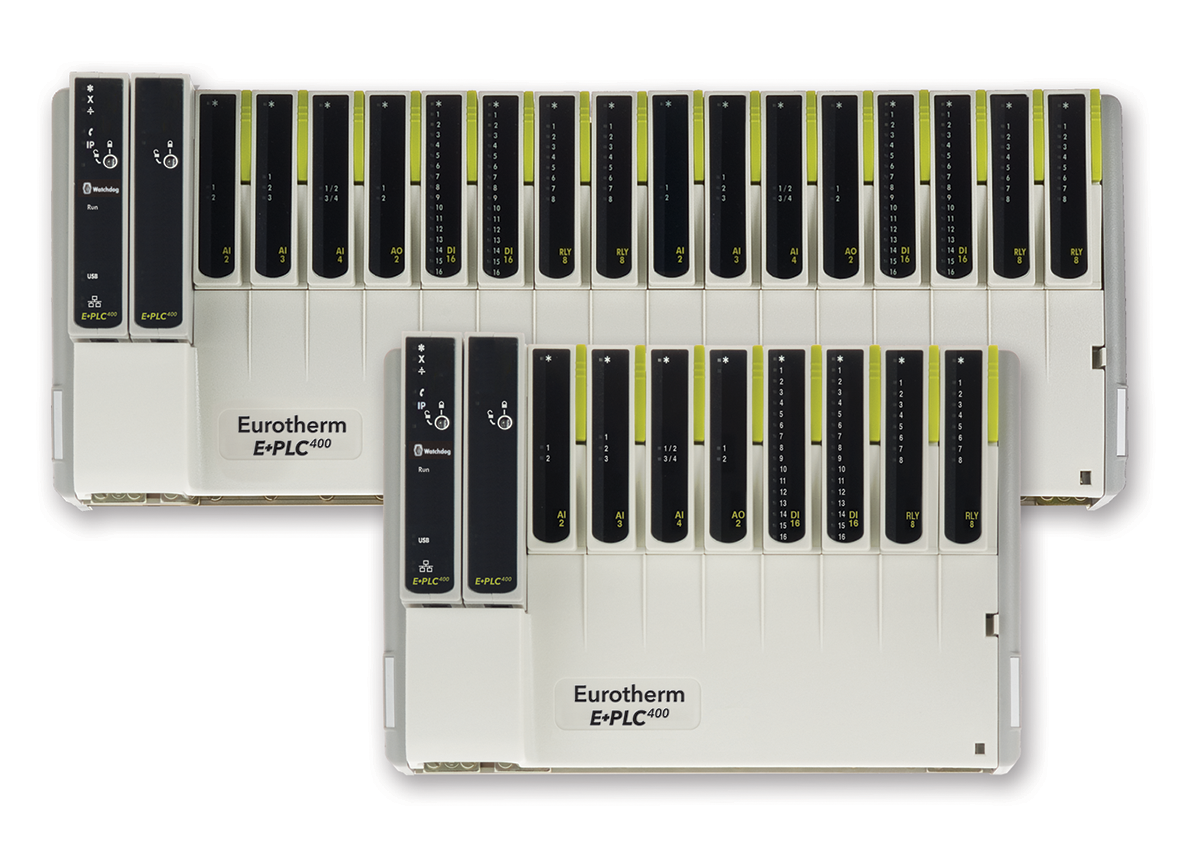
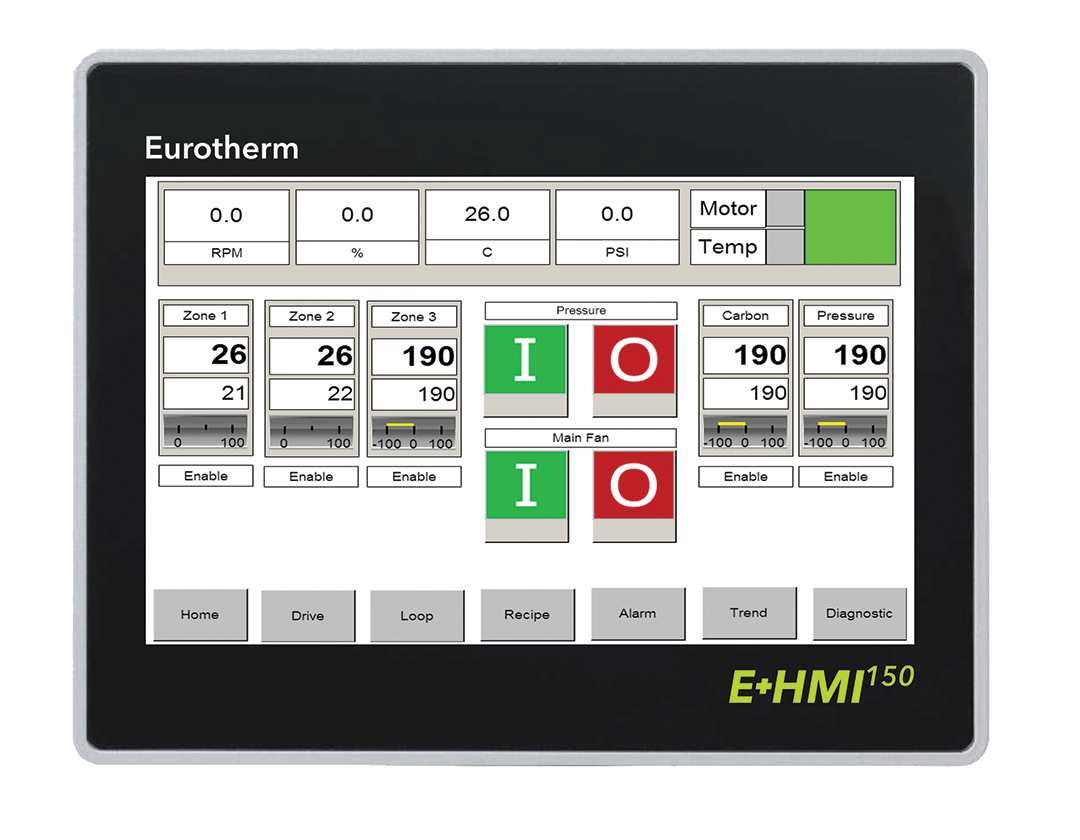
This is a modular combination PLC with selectable base and can be scaled to suit almost any application.
This option gives you precise control, setpoint programming and tamper resistant recording fully integrated within a PLC. It minimises engineering and commissioning costs while maximising process performance.
For large scale integration of analogue loops, or building management systems (BMS) and environmental management systems (EMS) the T2750 would be considered.
High Performance Din-Rail Mount PID Loop Controller
The Eurotherm Mini8 Loop Controller is high performance Din-Rail mount PID loop controller, which is very affordable.
The Mini8 loop controller has a modular design, which makes it the perfect solution for both simple and complex applications alike.
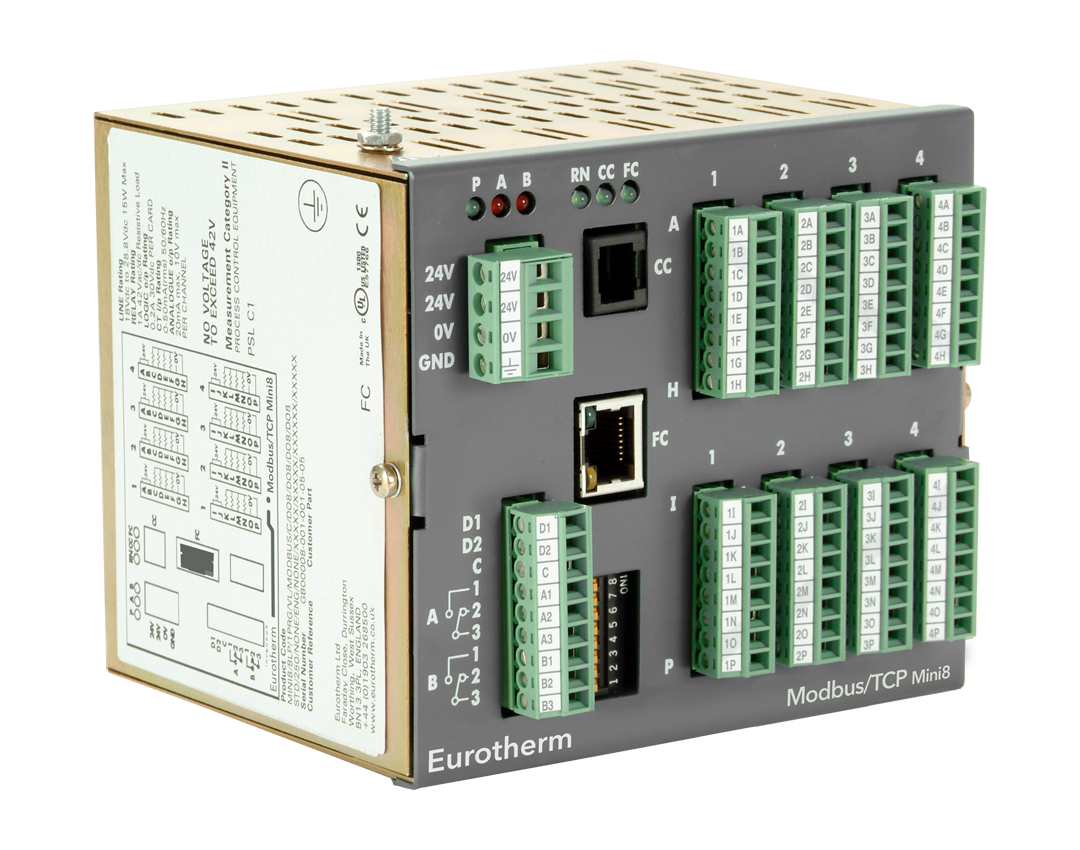
Example of Application in Australia
The Mini8 is used by one of Australia’s leading scientific research institutions.
We were originally contacted by the institution for a quote on a number of Eurotherm 3504 PID controllers.
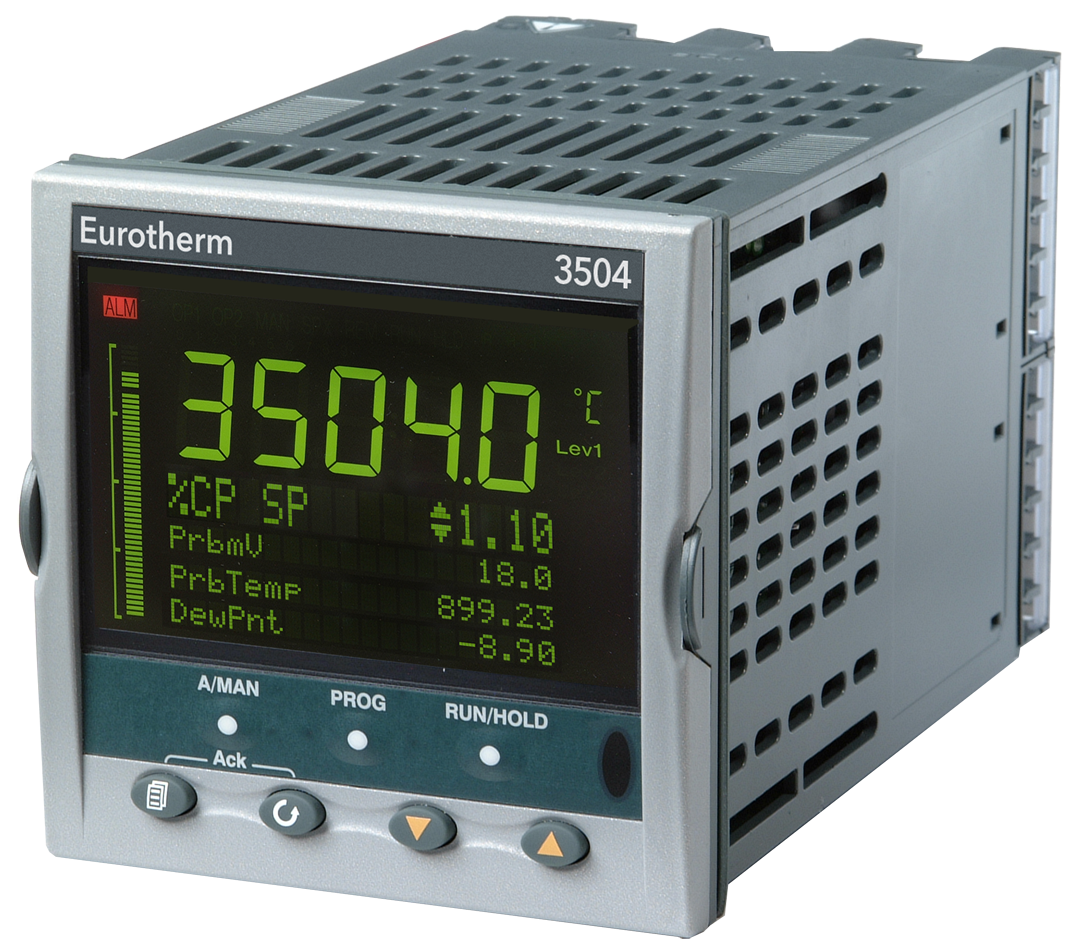
The number of units being asked for meant that this would have been a considerable purchase and ADM thought it appropriate to confirm the institution’s requirements before they committed to such a high level of expenditure.
It is in ADM’s DNA to offer high quality solutions, rather than make a sale at any cost.
Application Requirements
During our conversations with the institution, two key points emerged.
First of all, the application did not require a localised display as all data was to be captured by the SCADA system.
Secondly, the application involved multiple loops and tight integration across the loops was highly desirable.
The 3504 is a dual loop controller with a built-in display.
Rather than buying multiple 3504 controllers, ADM suggested that the customer opt for the Eurotherm Mini8 instead.
Of course, the most obvious saving for the institution was not having to paying for multiple visual display units that they were not going to use.
The modular design of the Mini8, meant that it could easily be scaled up to control the number of loops required. In fact, the Mini8 can control up to 16 loops.
I/O Options Available
There are a number of different I/O cards available including:
- 8 channel digital output
- 8 channel relay output
- 8 channel and 4 channel 4-20mA output
- 8 channel and 4 channel TC input
- 8 channel logic input
- 4 resistance thermometer inputs (PT100)
- 4 resistance thermometer inputs (PT1000)
- 3 channel current transformer input
Integration with PLC, or Higher-Level Control System
Integrating the Mini8 loop controller with a PLC, or higher-level control system is made easy by the number of communication protocols supported:
- Modbus RTU
- DeviceNet
- Profibus DP
- Ethernet
- Ethernet I/P
- EtherCat
In this particular application the research institution uses the Mini8 as a slave I/O interface to the existing control and monitoring software. It controls the loops according to the setpoints out of the SCADA system.
As all the loops are controlled by one Mini8 installation, tight integration across all of the loops is relatively easy to achieve. To do this with multiple dual loop controllers would have been much harder to set-up and may not have resulted in the same level of integration as offered by the Mini8.
Easy Set-up and Configuration
Another useful feature of the Eurotherm Mini8 is the iTools software with graphical wiring. This makes the configuration of the Mini8 remarkably easy.
30 wires are provided as standard, which is adequate for a relatively straight forward installation. For more complex applications there is the option to purchase either 120, or 250 wires.
Application Summary
Instead of simply quoting the research institution, ADM took the time to discuss the requirements of the application, in order to gain a good understanding of what was actually needed.
The Mini8 offered a far more cost-effective solution, which was better suited to the application technically.
The institution did not pay for features they did not need, such as the visual display unit on the 3504s. Yet they ended up with a solution, which offered them the level of integration across the loops that they needed and could easily communicate with their existing control and monitoring software.
PID Controller for Precision Control of Heating Process
Many industrial processes require the precise control of heating elements. Where this is the case, a good quality PID controller is required.
Simple on / off heating controls have little, or no ability to allow for time lag. Typically, the heating element is switched off when the set-point is reached. However, the latent energy in the heating element means the temperature continues to rise after the element has switched off.
This can cause a problem.
For example, some products like Nylon do not like to be overheated. And when it comes to food and beverage production it is highly desirable to maintain a constant temperature throughout production, otherwise there is a variation in the quality and flavour of the end product.
Eurotherm’s fast PID control gives you accurate control of the heating process, ensuring that the temperature doesn’t rise past the set-point.
Eurotherm’s PID algorithm delivers industry-leading response time to set-point change or process disturbance. The speed of response means time and energy is not wasted waiting for operating temperature to be reached, while minimising the overshoot and oscillations common in many PID implementations.
Eurotherm offers a wide range of PID controllers, including the new and highly advanced Eurotherm EPC3000.
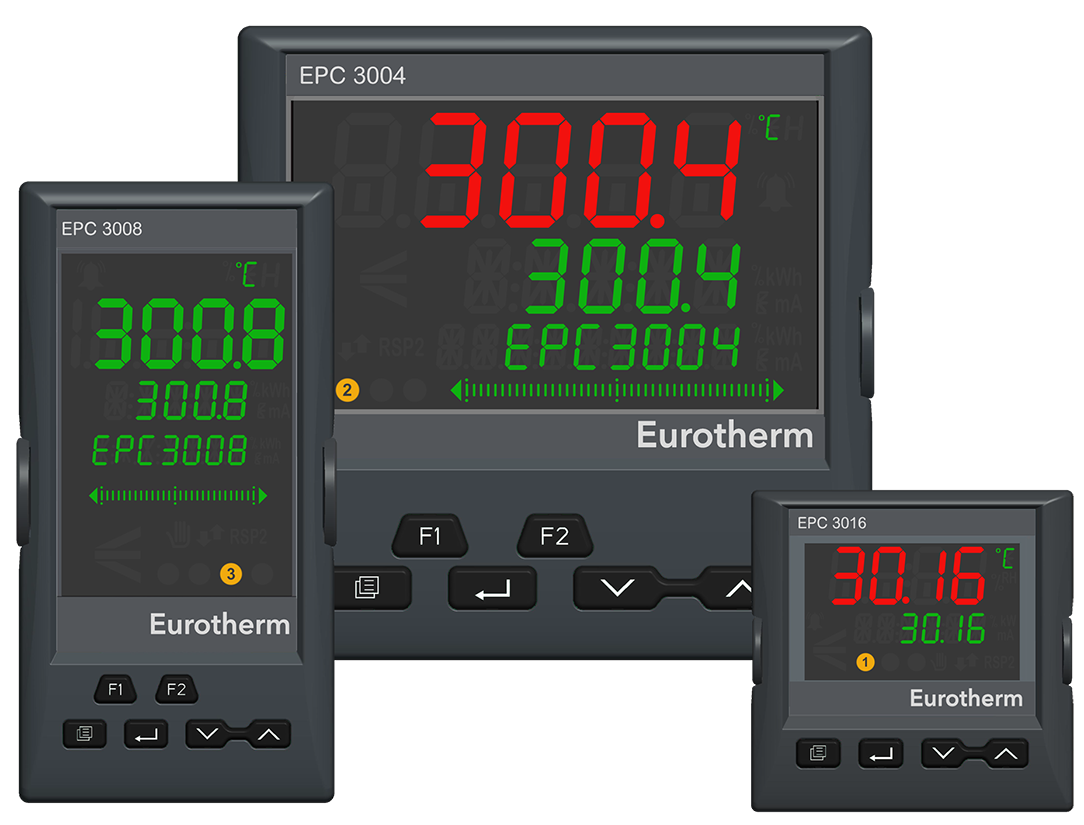
Of course, you may not need something quite as advanced as the EPC3000.
For example, you may not need secure communications, because your process runs completely off line.
If this is the case, then it could be that the Eurotherm 3200 Series PID controllers would be better suited.
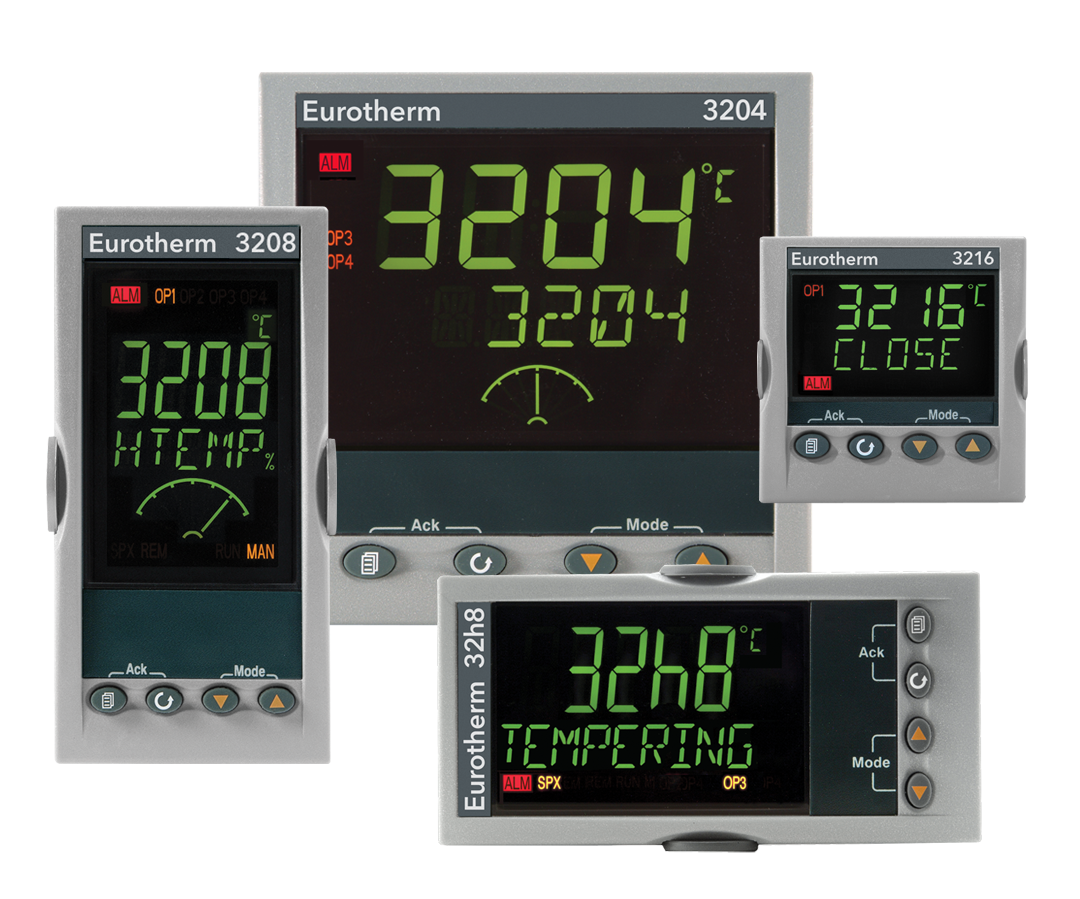
They will still deliver highly accurate control of your heating process, but not have a suite of features that you are unlikely to use.
Eurotherm PID controllers are highly flexible, scalable and very affordable.
Make sure you include Eurotherm, when researching what PID controllers would be best for the precise control of your heating processes.
SIL Process Controllers for Machinery Safety Control Systems
Both the Eurotherm EPC2000 and EPC3000 process controllers have been assessed to EN ISO 13849-1 Performance Level (‘PL’) ‘c’.
This is generally considered to be equivalent to SIL 1.
Under ISO 13849, the design of the safety system is based on the risk assessment performed by the manufacturer of the machine.
The risk assessment identifies the safety functions required to mitigate risk and the performance level the functions need to meet to adequately mitigate the identified risks.
The performance level of a function is determined by the architectural characteristics of the machine, the MTTFd (mean time to dangerous failure) of the components and system and the average diagnostic coverage implemented in the system.
The Eurotherm EPC2000 and EPC3000 controllers can be used in a machine to control its safety features.
The ‘Performance Level’ mentioned above is used by the machine designer as part of the risk assessment. It must be stressed that the responsibility for the safety of the machine rests with the machine designer.
The below table shows the 5 performance levels under EN ISO 13849 and the average probability of a dangerous failure for each level:
EN ISO 13849 is a safety standard which applies to machinery control systems that provide safety functions.
Performance Level (PL) | Average Probability of Dangerous Failure per Hour |
---|---|
a | ≥ 10-5 to < 10-4 |
b | ≥ 3 x 10-6 to < 10-5 |
c | ≥ 10-6 to < 3 x 10-6 |
d | ≥ 10-7 to < 10-6 |
e | ≥ 10-8 to < 10-7 |
NOTE: Beside the average probability of dangerous failure per hour, other measures are also necessary to achieve the PL. |
Performance Level C (PLc) is generally considered to be equivalent to SIL 1.
Why ADM?
Christopher Lonergan, our Eurotherm Product Leader has more than 30 years’ experience working with the Eurotherm product range. Christopher will take the time to get a full understanding of your application, so that the most cost-effective solution can be selected.
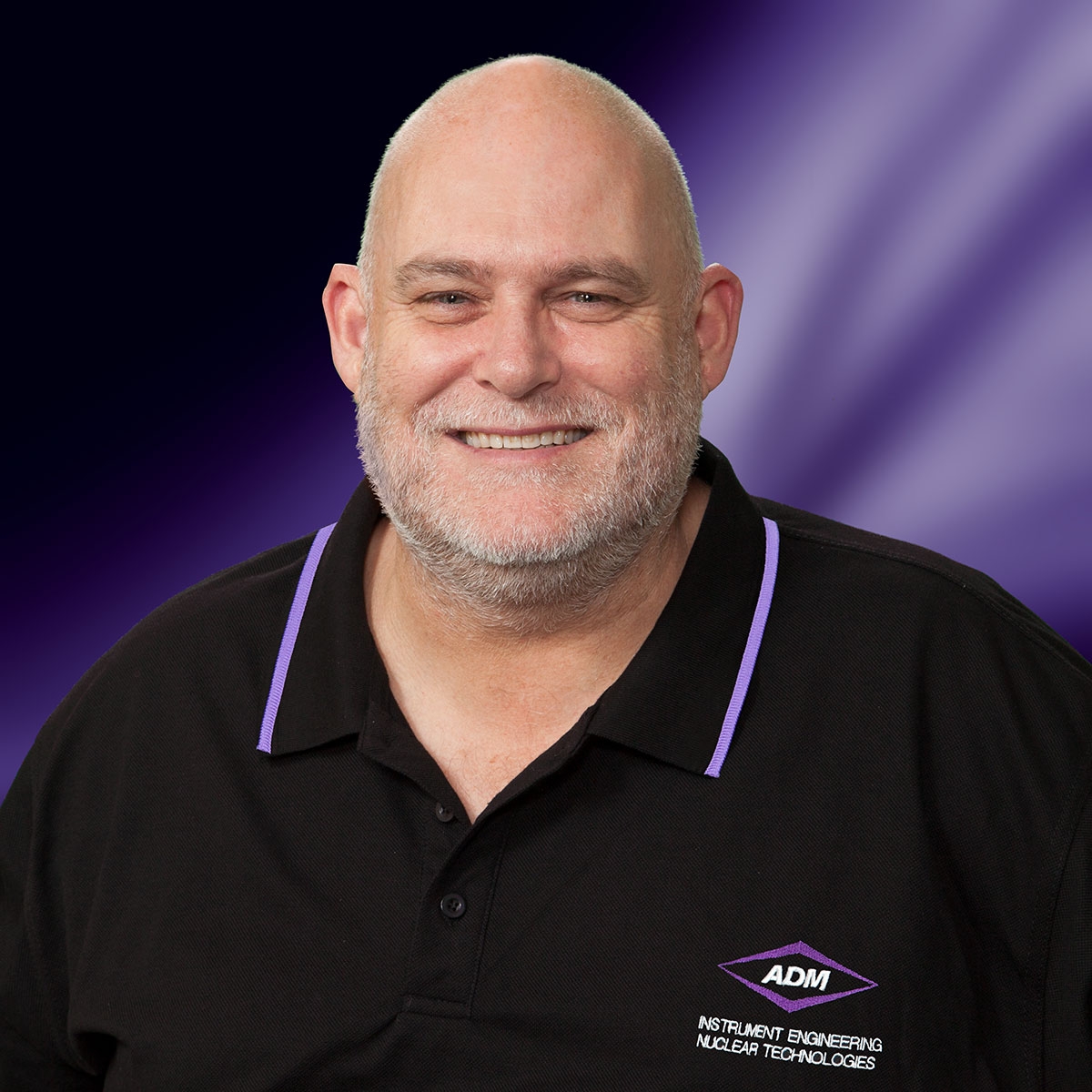
We are not about a sale at any cost. If Eurotherm is not the right fit, we will say so.
If you are looking for a PID loop controller, then contact ADM Instrument Engineering.
WAS THIS INFORMATION USEFUL?
Why not share it with you industry peers on LinkedIn? Simply click on the blue LinkedIn share icon below.
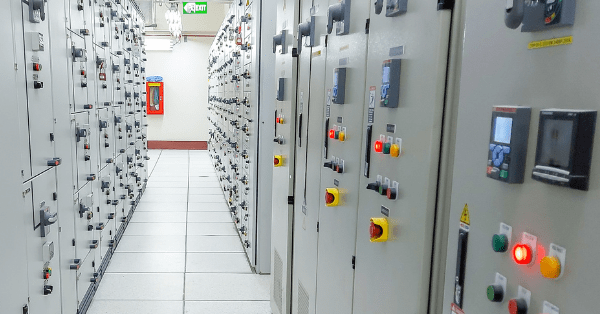