Pressure Sensors for Hydraulic Systems
This blog post discusses the factors that need to be considered when selecting a pressure sensor for use in hydraulic systems.
Hydraulic cylinders are ubiquitous in industrial and mobile applications. For example mining, petrochemical, marine, automotive, construction, defence and aerospace. They are useful in generating extremely high forces to move parts or levers of a machine by means of hydraulic oil under high pressure driving a piston and rod. The ancient Egyptians would certainly have benefited from them building the pyramids, saving enormously on manpower.
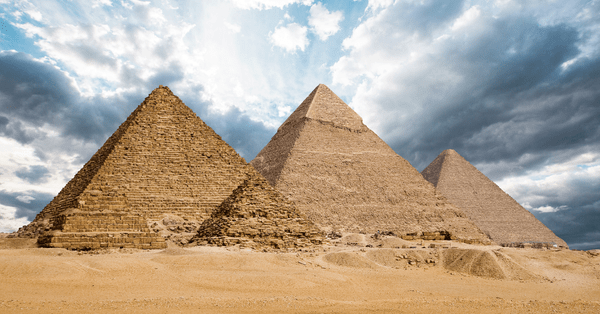
To measure the force applied by the hydraulic cylinder a load cell could be used, but in many cases, it is more convenient using a pressure transmitter connected to the hydraulic system. A pressure transmitter has a specially engineered diaphragm designed to deflect linearly with increased pressure. A strain gauge, which is inherently fragile, is bonded to the diaphragm to provide an electrical output signal proportional to the applied pressure.
To derive force from the pressure measurement (in Pascals) we also need to know the surface area of the piston (m2m2), which is obtained from hydraulic cylinder datasheet, and use the following equation.
Force (N) = Pressure (Pa) * Area (m2)
Hydraulic applications tend to be highly dynamic with rapid changes of force and direction of movement controlled by valve actuators directing the flow and pressure of the oil.
Combine this with applications in some of the harshest environments like hot dusty deserts or deep underground mines, and it is not difficult to realise hydraulic pressure transmitters need to be not only accurate, but adequately robust to cope with extreme hard labour. For example, they must endure vibration & mechanical shock, ultra-high operating pressures, overpressure, pressure spikes and high temperatures.
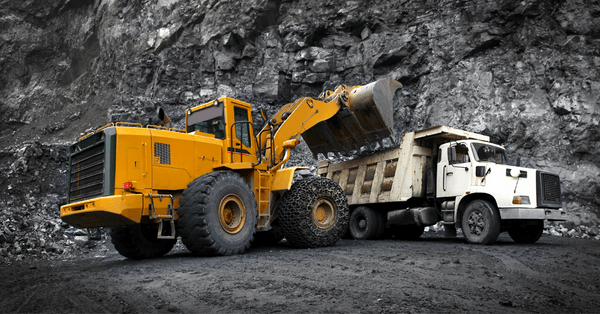
Like the piston, the pressure transmitter diaphragm takes the full force of the hydraulic oil, and at maximum operating pressure, it deflects approx. 80 microns (0.080 mm) for the strain gauges to give the maximum output.
For the pressure transmitter to continue providing an accurate measurement during its lifetime, it is critical not to exceed the diaphragm’s elastic limit. Generally, pressure transmitters are designed to withstand 150 – 200% the operating pressure, called the over pressure limit, which is still with the diaphragm’s elastic limit. Beyond that, the diaphragm will permanently deform rendering the pressure transmitter unserviceable. In hydraulic systems, this could lead to a fatal outcome.
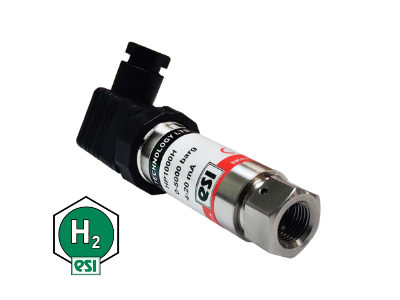
When pressure is applied to a liquid its temperature rises causing it to expand, thus increasing the pressure and in turn the temperature. When the hydraulic system is working hard, high oil temperatures could reduce the accuracy of the pressure transmitter if the maximum operating temperature of the sensor is exceeded. Maximum operating temperature of the pressure transmitter is something to be mindful of when selecting something suitable for the application.
One of the worst operational occurrences to ruin the health of a pressure transmitter are pressure spikes, which are very short duration high frequency pulses, sometimes referred to as ‘water hammer’. These pulses typically occur when oil is being pumped quickly only for a valve actuator to shut suddenly.
An example of this phenomenon is one’s washing machine filling with water and the valve closing quickly the moment the water has reached the required level.
Water, like hydraulic fluid, is incompressible and when it is moving it has a certain momentum. To bring the flow to a stop, that momentum must be opposed. When it comes to a quick stop with nowhere to go and carrying that momentum, pressure in the pipe rises rapidly, several times that of the operating pressure of the system. This sends a shock wave through the house or building, and if left unattended over time, may result in a burst water pipe and broken pressure gauges.
In hydraulics, this can be catastrophic. However, mitigating the effect of water hammer is nigh impossible when selecting a suitable sensor as it is generally because of adverse machine operation.
Hydraulic systems are predominantly used on high value equipment; and machine down time can cost owners a lot of lost revenue. Therefore, it is imperative to select the most appropriate pressure transmitter for the high pressures involved and the harsh environments that are present in hydraulic applications.
ADM Systems offers several pressure transmitters product that are specifically designed for hydraulic applications, and we stock the most common pressure ranges (100 to 1000bar) found in hydraulics applications, here in Australia.
If you would like assistance in selecting a suitable pressure sensor for your hydraulic application, please do not hesitate to contact ADM Systems.
