POSITAL’s Absolute and Incremental Encoders: The Unsung Heroes of Precision
Did you ever wonder how robots move their joints with precision, or how the axle wheels of trains accurately run on track? What do these two have in common with conveyor belts, sushi trains and crane hoists?
Encoders.
These small yet mighty gadgets pack a punch when it comes to motion feedback and control.
What is an Encoder?
An encoder is a type of sensor that converts motion into electrical signals that can be interpreted by electronic control devices, such as a counter or a programmable logic controller (PLC). These signals provide position, speed, count, or direction feedback, which enable precise control of machinery.
Understanding the Differences Between POSITAL’s Absolute and Incremental Encoders
POSITAL has two types of encoders: absolute and incremental.
IXARC POSITAL absolute rotary encoders can provide unique position values from the time they are switched on. Since all these systems correspond to a unique code, the exact positioning is determined by scanning the coded element. Even movements that occur while the system is turned off are translated into accurate position values once the encoder is powered up again.
Another feature of absolute rotary encoders is the high number of variations. Absolute encoders can either be single turn or multiturn with different resolutions and communication interfaces. There are also thousands of mechanical and connection configurations to choose from to meet specific applications.
This is particularly useful for railway systems to determine not just the speed, but the position of the locomotive itself.
IXARC POSITAL incremental encoders, on the other hand, generate an output signal each time the shaft rotates at a certain angle. The number of signals or pulses per revolution (PPR), defines the resolution of the device.
Each time the encoder is powered on, it begins counting from zero, regardless of where the shaft is. Therefore, initial homing to a reference point is necessary in all positioning tasks – both upon activating the control system, and whenever power to the encoder has been interrupted.
The internal components of incremental encoders are less complex compared to those of absolute encoders. This meets the need of most machineries requiring simple, cost-effective solutions while still providing accurate positioning, like machine tools and self-guided vehicles or Automated Guided Vehicles (AGV), for example.
POSITAL magnetic encoders can all be configured via the UBIFAST configuration tool, helping reduce inventory levels.
Do you need more information? Call ADM for technical advice and assistance. Our contact details can be found in this link.

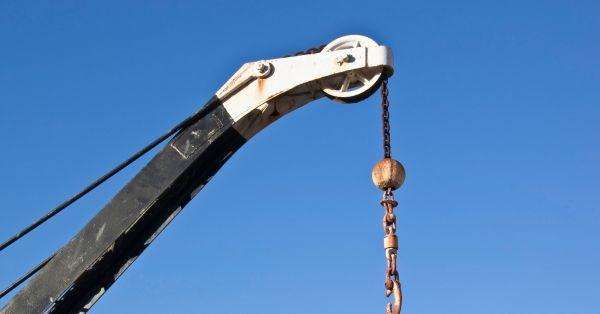