Measuring Liquid Ammonia Concentration with Process Refractometers
Ammonia plays a crucial role in multiple industries and applications. As global efforts intensify towards promoting environmental sustainability, addressing climate change, and achieving carbon neutrality, there is a growing emphasis on developing eco-friendly methods for Ammonia production and implementing efficient systems for its use.
How do we make Ammonia?
The process of creating Ammonia (NH3) requires the combination of two elements, Hydrogen & Nitrogen. Hydrogen and Nitrogen are extracted from two different sources through their own respective systems before being combined in synthesis producing Ammonia.
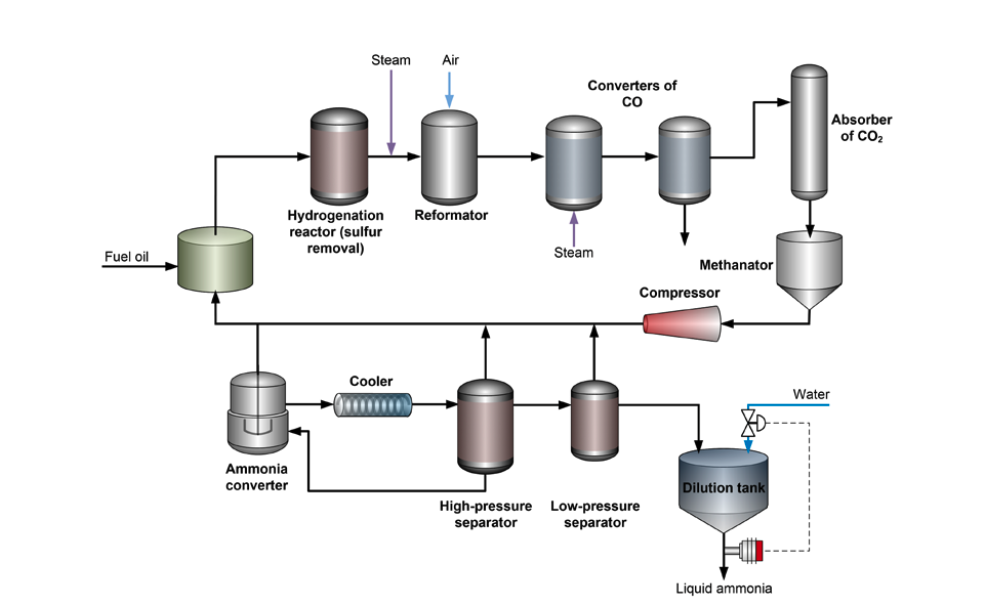
What is the future of Ammonia manufacturing?
Since the early 1900s, Ammonia traditionally has been produced via the Haber process. The raw material is natural gas or fuel oil (naphtha), which produces hydrogen (H2) for the steam reforming process. But with the need to decarbonize in line with meeting net zero initiatives, alternate sources of hydrogen are being researched and developed. One such method is to use an Electrolyser powered by renewable energy (Solar PV + batteries, Hydro etc) to generate hydrogen from water.
If this can be done at scale, one of the world's most important chemicals can continue to be produced significantly lowering CO2 emissions for a cleaner world. Whilst Ammonia is key to manufacturing ammonium nitrate fertilizers for increased food production, the uses for Ammonia may extend past the farm into fuel for ships and co-generating electricity by combustion with coal.
But this will depend on the ability to economically sequester the CO2 gas produced.
How do we make Ammonia useable? Liquefying Ammonia!
Different applications require Ammonia to be applied in various forms, for example, as a fuel source it may be required to stay in a gaseous state, whereas for Sanitation, Cleaning and Fertilizer manufacturing, a liquid form is required. In this instance, cooling and liquefaction are added to the end of the Ammonia synthesizing stage to form aqueous Ammonia or Ammonium Hydroxide.
To manufacture Ammonium Hydroxide, it is important to accurately monitor and control the liquid concentration. This is best achieved with an in-line Process Refractometer such as the new POLARIS Series from Vaisala.
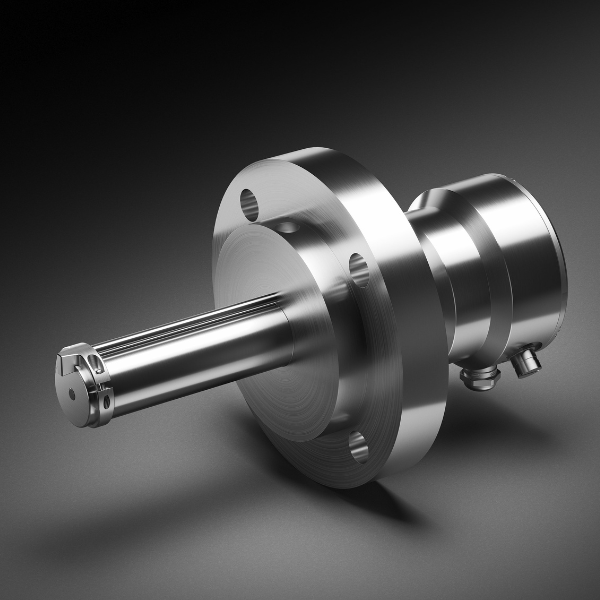
Measuring Ammonia Liquid Concentration: Instrumentation and Installation
Vaisala Polaris Process Refractometer PR53GP measures the concentration of liquid Ammonia after dilution. The final concentration of Ammonia is typically around 25 % with measurements taken at ambient temperature.
The refractometer can be easily calibrated either to read NH3 (Ammonia-in-water) or NH4OH (ammonium hydroxide) in water. The refractometer provides direct 4-20 mA and RS485 output signals that can be used for automatic control of the dilution process. The signal from the refractometer controls the water feed valve, thus ensuring a correct concentration level in the final product. In certain cases, steam prism wash may be recommended.
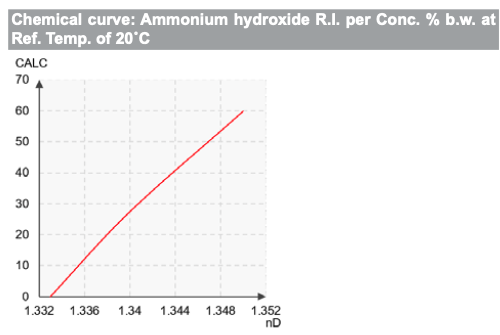
Instrumentation Description
The PR53-GP Process Refractometer is a general industrial refractometer for pipes and vessel installations. The PR53-GP can be installed with 2, 3 and 4-inch flange and 3-inch Sandvik L-coupling process connections and a variety of flow cells for pipe sizes of 1 inch and larger.
User Interface
INDIGO520 is an advanced HMI option that offers a local display of the refractometer measurement and diagnostics data. It also provides a web interface for remote viewing.
Automatic Prism Wash
Prism wash with steam (optional). The components of a steam wash system are a sensor with an integral steam nozzle mounted at the sensor head, a shut-off valve for the steam line and an indicating transmitter equipped with relays to drive the wash valves.
Measurement Range
Refractive Index (nD) 1.3200 – 1.5300, corresponding to 0-100 % by weight.
Why Use an In-line Process Refractometer for Concentration Measurement?
The measurement is based on the optical measurement of the refractive index (RI). The RI can be measured from essentially any liquid, and it is sensitive to only dissolved material. Bubbles, particles, or colours do not affect the measurement.
Vaisala has a library of over 500 concentration curves to suit almost any application. Use a factory pre-installed concentration curve or customize it to suit the application for the measurement units you prefer.
Easy to install using a variety of standard flange connections either directly into the pipeline or using an optional flow cell.
Maintenance-free operation with drift-free calibration. Traceable verification can be easily performed using Refractive Index fluids.
Got Questions? Get in Touch Today!
If you’re looking for a reliable liquid measurement solution for your installation, Contact the ADM Engineering Team today!
Have a look at our range of Inline Process Refractometers here.
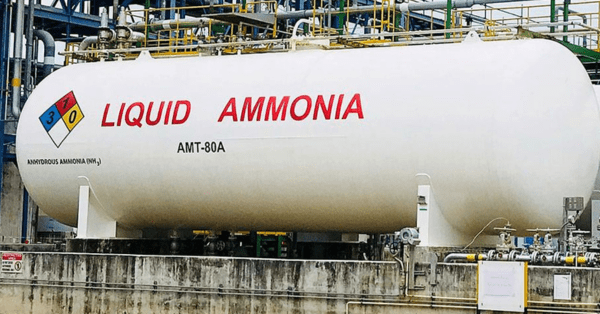