Common Warnings, Trips, Faults, and Failures in Invertek Drives: Causes and Solutions
Variable frequency drives (VFDs) are powerful tools for controlling motor speed, torque, and efficiency in industrial applications. However, like any complex equipment, they can encounter issues if not correctly operated or maintained. Invertek drives have built-in protections that raise warnings, initiate trips, or signal faults to prevent damage. In this article, we dive deeper into the causes behind these warnings, trips, faults, and failures, and how to address them.
Warnings: Early Signs of Potential Trouble
Warnings are indications that something isn’t quite right but hasn’t yet reached a critical stage. When a warning is triggered, the drive continues to operate but signals that an issue is developing. Ignoring warnings can lead to more severe issues like trips or faults.
Common Causes of Warnings:
Overloading the Motor or Drive: Warnings often arise when the motor or drive is running above its designed load capacity. Overload conditions can be caused by unexpected changes in the mechanical load (e.g., a conveyor jam), improper sizing of the motor relative to the application, or long acceleration/deceleration times.
Overheating: Both the motor and the drive can overheat due to excessive current draw or poor ventilation. Internal components, like power semiconductors, generate heat during normal operation, and without proper cooling, the drive’s temperature will rise beyond safe limits.
Cooling System Issues: Dust buildup, blocked filters, or malfunctioning cooling fans can restrict airflow, causing the drive to overheat. Similarly, if the drive is installed in a hot, enclosed area with insufficient ventilation, internal temperatures can rise quickly.
Solution: To resolve warnings, check the mechanical load and ensure the motor is correctly sized. Address any blockages in the drive's cooling system and verify that fans are functioning. If the motor or drive is persistently overheating, consider reducing the load or adding external cooling.
Trips: Automatic Shutdown to Prevent Damage
Trips are designed to shut down the drive when conditions become too dangerous for continued operation. A trip immediately stops the drive to protect the system, with a fault code displayed to indicate the cause.
Detailed Causes of Trips:
Overcurrent Trip (O-I): This happens when the current spikes rapidly due to an electrical short, a jammed motor shaft, or a severe overload situation. It can also occur during startup if the load is too heavy or the acceleration is too rapid.
Motor Overload Trip (I_t-trp): This trip is triggered when the drive detects that the motor is drawing more current over time than its rated capacity allows. Causes include mechanical overloads, incorrect motor parameter settings, or poor ventilation around the motor.
Drive Overload Trip (O-t): The drive is designed to handle temporary overloads, but sustained overloading will lead to a trip. This is common during peak load conditions, or if the motor is accelerating or decelerating too quickly for its rating.
Undervoltage Trip (U-volt): When the supply voltage drops below the drive’s specified limits, typically caused by unstable power sources or power cuts, this trip activates. In many cases, undervoltage trips are logged due to sudden power disconnections while the drive is operating.
Overvoltage Trip (O-volt): Overvoltage trips occur when the DC link voltage in the drive exceeds its safe operating range. This is usually the result of regeneration, where the motor acts as a generator, feeding energy back to the drive during rapid deceleration or when lowering a load. High-inertia applications, such as fans or conveyors, are prone to generating excess energy.
Regeneration During Deceleration: When stopping a high-inertia load, the kinetic energy has nowhere to go but back into the drive, increasing its internal voltage. In extreme cases, this can cause the drive to trip to protect itself from electrical damage.
Under Temperature Trip (U-t): Drives are sensitive to both high and low temperatures. If the drive's environment is too cold (below -10°C), internal components like semiconductors can become sluggish, leading to a trip.
Solution:
For overcurrent or motor overload trips, inspect the motor for blockages or short circuits, and verify that load parameters are correctly set. If the trip is caused by overvoltage, consider adding a braking resistor or adjusting the deceleration rate to reduce the energy fed back into the drive.
Ensure the drive operates within its voltage and temperature specifications, and check that the power supply is stable to prevent undervoltage trips.
Faults: System Configuration and Control Signal Issues
Faults are different from trips because they are often linked to incorrect configuration or communication issues rather than direct mechanical or electrical failures. Faults may prevent the drive from operating correctly, but they don’t always indicate an imminent risk of damage.
Common Causes of Faults:
Parameter Default Fault (P-deF): This fault occurs when the drive’s parameters are reset, either accidentally or as a result of a power glitch. In some cases, users may reset parameters while troubleshooting or during commissioning, which can inadvertently lead to a fault.
ImageExternal Trip Input Fault (E-triP): The drive may be programmed to respond to external control signals, such as an emergency stop button or limit switch. When these signals are triggered, the drive stops and displays a trip fault.
Motor PTC Fault (F-Ptc): The motor PTC (Positive Temperature Coefficient thermistor) is embedded in the windings to monitor the motor’s temperature. If this sensor fails or overheats, it will signal the drive to trip to protect the motor.
4-20mA Signal Loss Fault (4-20 F): The drive may be set up to receive a 4-20mA control signal from an external device, such as a pressure or flow sensor. If the wire breaks or the signal drops, the drive will raise a fault.
Phase Loss Fault (P-LOSS / Out-F): Three-phase input drives monitor the incoming power. If one of the three phases is lost (due to a power supply issue or blown fuse), the drive will trip to prevent damage to the motor and drive.
Inhibit Fault (INhibit): Some drives (especially the P2 and Eco series) have a safety feature called Safe Torque Off (STO). If the STO inputs are not properly connected or bridged, the drive will remain in a disabled state and raise an inhibit fault.
Image
Solution:
Correct parameter settings, check control signal wiring, and ensure that external sensors and inputs are properly connected. For motor PTC faults, ensure the sensor is functioning correctly and that the motor isn’t running too hot.
Inhibit faults can usually be resolved by ensuring the Safe Torque Off inputs are properly connected, allowing the drive to operate.
Failures: When Things Go Very Wrong
While warnings, trips, and faults are relatively common and often manageable, a complete drive failure is rare. Modern Invertek drives are designed to be highly reliable, but in some cases, contamination or misuse can lead to total failure.
Common Causes of Failures:
Contamination: Dust, moisture, or chemical exposure can infiltrate the drive enclosure, causing corrosion or short circuits. This is especially common when drives are installed in harsh industrial environments without adequate protection (e.g., in an IP55-rated enclosure).
Fig 1: Dust build-up inside drive Fig 2: Dust blocking airflow causing fan failure Misuse: One of the most common causes of drive failure is improper wiring, such as connecting the input terminals to the output, which can cause severe electrical damage.
- Severe Overloads: Despite built-in protections, extreme conditions like a sudden, unmanageable overload or a large voltage spike can bypass the drive’s trip mechanisms, leading to component failure.

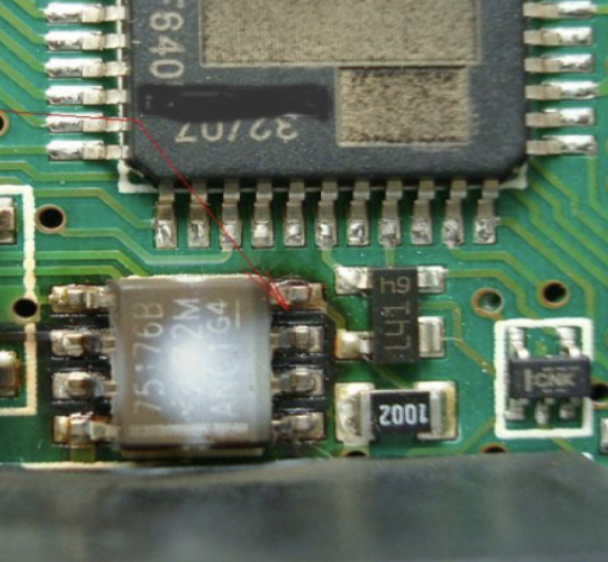
Solution: Prevention is key to avoiding drive failures. Ensure that the drive is installed in a clean, dry environment with adequate protection against dust and liquids. Regular maintenance, such as cleaning filters and checking for contamination, can also help. Make sure wiring is correct during installation to avoid severe misuse, and use appropriate fuses or surge protection to guard against electrical spikes.
Conclusion
Invertek drives come with extensive protective features to safeguard both the drive and motor from damage. Understanding the common causes of warnings, trips, faults, and failures allows for timely troubleshooting and preventive maintenance.
While many issues can be resolved with simple adjustments to load conditions or cooling, more serious problems like incorrect wiring or phase loss require careful attention to avoid complete drive failure. By familiarizing yourself with the causes behind these protective measures, you can maintain optimal performance from your Invertek drive and minimize downtime in your operations.
Do you require additional information on variable speed drives? Contact ADM here for technical support and guidance.
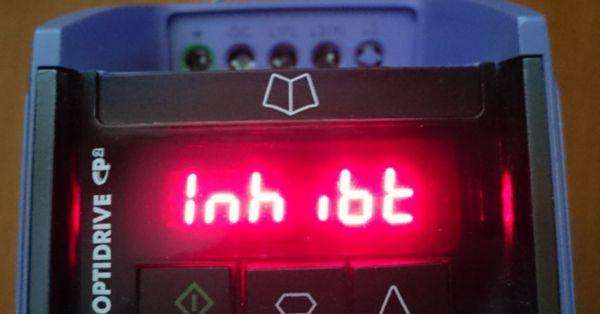